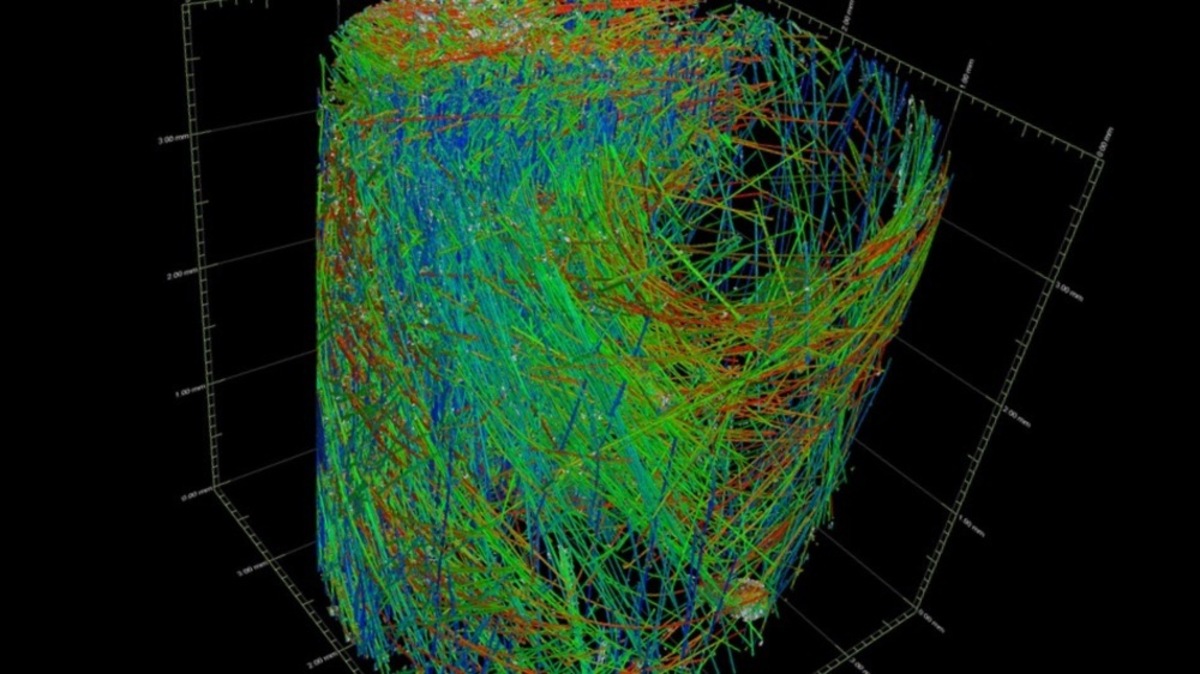
©Faserinstitut Bremen e. V.
A Deep Look Inside
The material research carried out in and by the university is done with a high-resolution X-ray microscope of the most recent generation
It is a piece of equipment that the MAPEX Center for Materials and Processes at the University of Bremen is very proud of: the ZEISS Xradia 520 Versa. What may mean nothing to laypersons, makes the jaws of specialists drop, as this device is an X-ray microscope of the newest generation, with which it is possible to observe minute dimensions. It has even been made more powerful in Bremen by means of diverse additions. In the field of new material development, the microscope is opening entirely new opportunities for the material sciences in the hanseatic city.
Dr. Wolf-Achim Kahl is impressed. After several years’ work with a computer tomograph in the Faculty of Geosciences, he has been the responsible laboratory manager for the 3D X-ray microscope of the MAPEX research network for several months now. A large device that the University of Bremen acquired as part of a German Research Foundation (DFG) initiative at the beginning of 2017 and which now offers entirely new opportunities for the investigation of the internal structures of all types of materials. “We can take a nondestructive look into ceramics, fiber composite materials, metal or biological materials, and much more, and that at a magnitude of less than a thousandth of a millimeter,” says Kahl. The insights with the XRM– the abbreviation of “X-ray microscope”– are even more detailed, more specific, more conclusive. “It is a dream for material scientists because you get results that are clearly more precise, and you can carry out research on far more detailed issues,” according to Kahl.
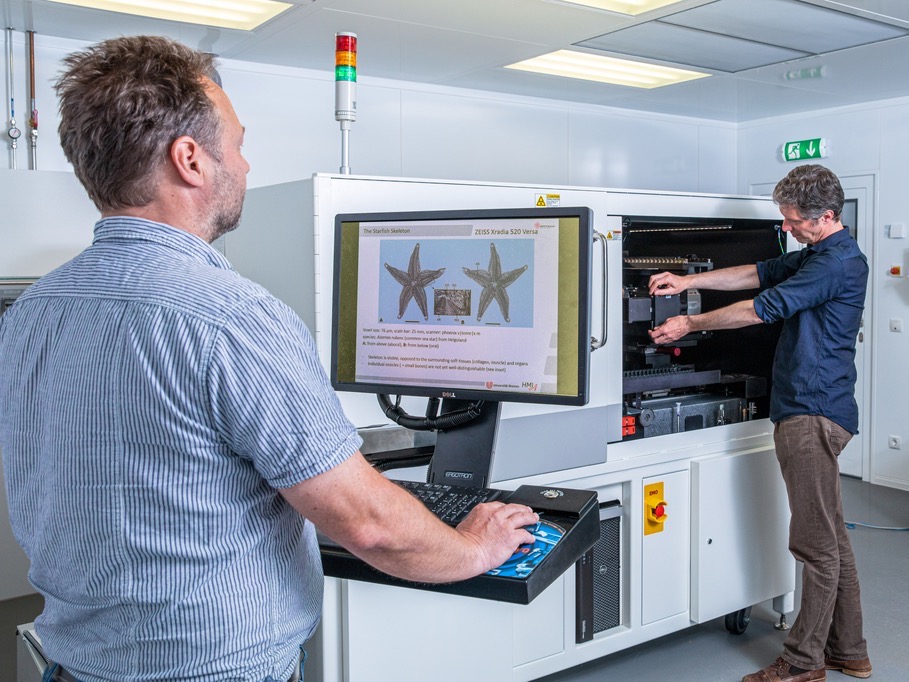
©Matej Meza / Universität Bremen
The Highly Resilient Legs of the Grasshopper
What is relatively new for Wolf-Achim Kahl, is something that the physicist Oliver Focke from Faserinstitut Bremen e.V. (FIBRE) has experienced repeatedly: The amazement surrounding the capabilities of new large devices. Focke has been setting up the XRM for operation since 2017 and has carried out varying types of measurements. “One of the first projects came from the field of bionics. Together with the B-I-C–Biomimetics-Innovation-Centre at Bremen University of Applied Sciences, we examined the exoskeletons of insects.” Oliver Focke clearly remembers the X-ray of grasshopper legs. “The legs are very delicate but can withstand great amounts of strain in nature– several times their own-body weight,” explains Focke. The grasshopper legs are currently being examined for their adaptability with regard to mechanical strain whilst exposed to acceleration due to gravity in the DFG project “Effect of mechanical stress on insect exoskeletons.” “It is about recording possible differences in the structure and geometry of the legs as well as possible. We want to know what makes them so resilient and flexible but so light at the same time. Nature is often a model for technological developments.”
That is also shown by example of fiber composite materials, one of the most significant developments of the past decades. They belong to the group of materials that are often examined with the X-ray microscope in Bremen. The connection between light but extremely robust synthetic fibers and the fillers and adhesive materials in-between has created materials that have made many current applications possible. Light, hard, stiff: Fiber reinforced synthetic materials have taken over from light metals such as aluminum and are used today in many industries– for example air and space travel, the automobile industry and rail transport, wind power plants, but also in niche sectors. One needs to take a deep look inside in order to develop the best materials for varying applications: How do the fibers lie, where are tears, pores, or soiling, where is something not sticking quite right? “We take a look at everything that our colleagues produce,” smirks Oliver Focke. “We create thousands of cross sections that then allow for a 3D view when put together.”
Testing without Destroying
A very important aspect of the work with the X-ray microscope is the nondestructive testing, NDT in short. “That is often very important to material scientists. If, for example, there is a tear in a material, you can now have a good look with the XRM– the tear surroundings, the structures, the areas where adhesive maybe did not hold, and much more,” explains Wolf-Achim Kahl. That was not possible in the past: “One had to often cut out the damaged area or expose it to assess it microscopically. But in turn, said cuts led to a change in the actual damaged area and influenced it.” Nondestructive testing is a highly interesting research topic as the industry dreams of mass production without any interruptions. “Of course, they would find it great if quality supervision could take place directly in production,” knows Focke. Therefore, the integration of measuring methods in production processes is often a topic addressed by the MAPEX network.
“When I was looking at the most internal structures of a starfish, it suddenly reminded me of ceramic structures.”
With the high-definition microscope in Bremen it is basically possible to test all materials– even the surroundings of plant roots in ground substrate– and to make them visible without destruction. “Biologists are interested in how different microbes settle around a plant root, for example,” stated Wolf-Achim Kahl. Together with the German Maritime Museum in Bremerhaven, an entirely different object was also assessed: a clockwork-operated toy submarine from 1915. “The researchers wanted to take a look inside– obviously without destroying it– and find out how exactly the clockwork is constructed and how it works,” says Oliver Focke. He had another moment of enlightenment when he viewed a starfish from the North Sea with the X-ray microscope and was able to look at the impressive details: “It suddenly reminded me of ceramic structures and there were actually astonishing similarities. The solutions that nature has are always amazing.”
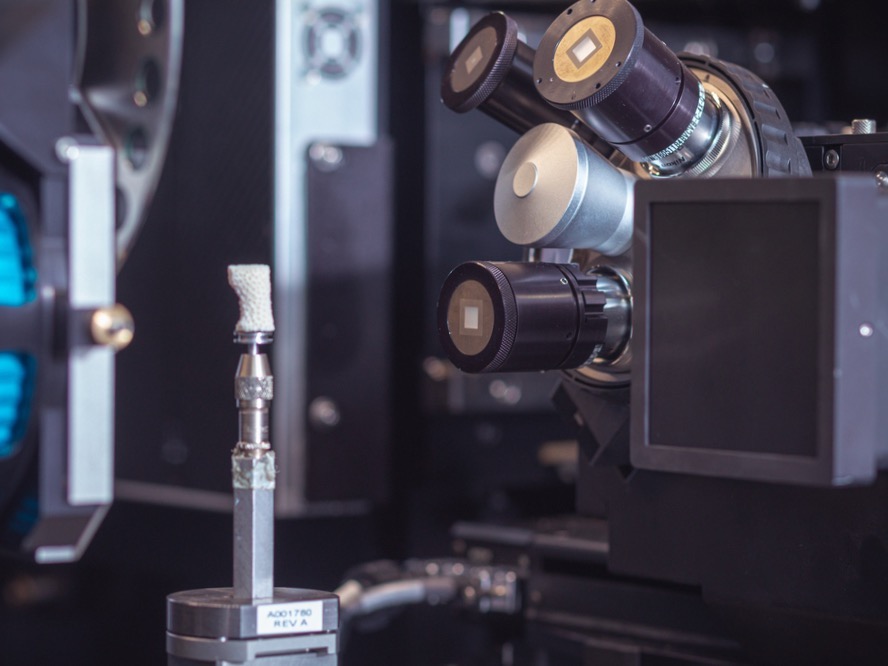
©Matej Meza / UniversitätBremen
How Do Raindrops Affect Wind Turbines?
Together with the Bremen Institute for Metrology, Automation and Quality Science (BIMAQ) and the Fraunhofer Institute for Manufacturing Technology and Advanced Materials (IFAM), the most recent research focused on which effect raindrops, sand, and ice have on the front edges of wind turbine rotor blades. Wait a second: Simple raindrops have an effect on modern wind turbines? “People underestimate it. The ends of the wind turbines are extremely quick. Those who have ever stuck their face out of a moving car when it is raining, know how much power raindrops have,” according to Oliver Focke. High-performance materials are expensive and must therefore be created in such a way that they keep for the longest time possible– the research, which is also carried out by the MAPEX network, helps to achieve this.
The X-ray microscope should not be seen in an isolated manner, but rather together with other high-performing analysis devices within the research network. “Many researchers do not even know what great devices and possibilities we have on campus. I am so pleased each time when I can connect people and contribute a little to the success of the work. I have often experienced that an inquiry for one individual measurement has ended in there being a new joint research project,” says Dr. Hanna Lührs, MAPEX’s scientific manager. Good examples of this are the above mentioned cooperations with the fields of bionics and the German Maritime Museum.
“In the past years, we have repeatedly managed to acquire new DFG funding for new large devices thanks to joint efforts. Alongside the X-ray microscope, our researchers will be able to use a state-of-the-art facility for 3D laser deposition welding and the newest generation of transmission electron microscope in the future.” The goal is to create a nationally significant large devices center for material analytics. With the MAPEX Core Facility for Materials Analytics project, the DFG is supporting the University of Bremen on this path for the next five years.