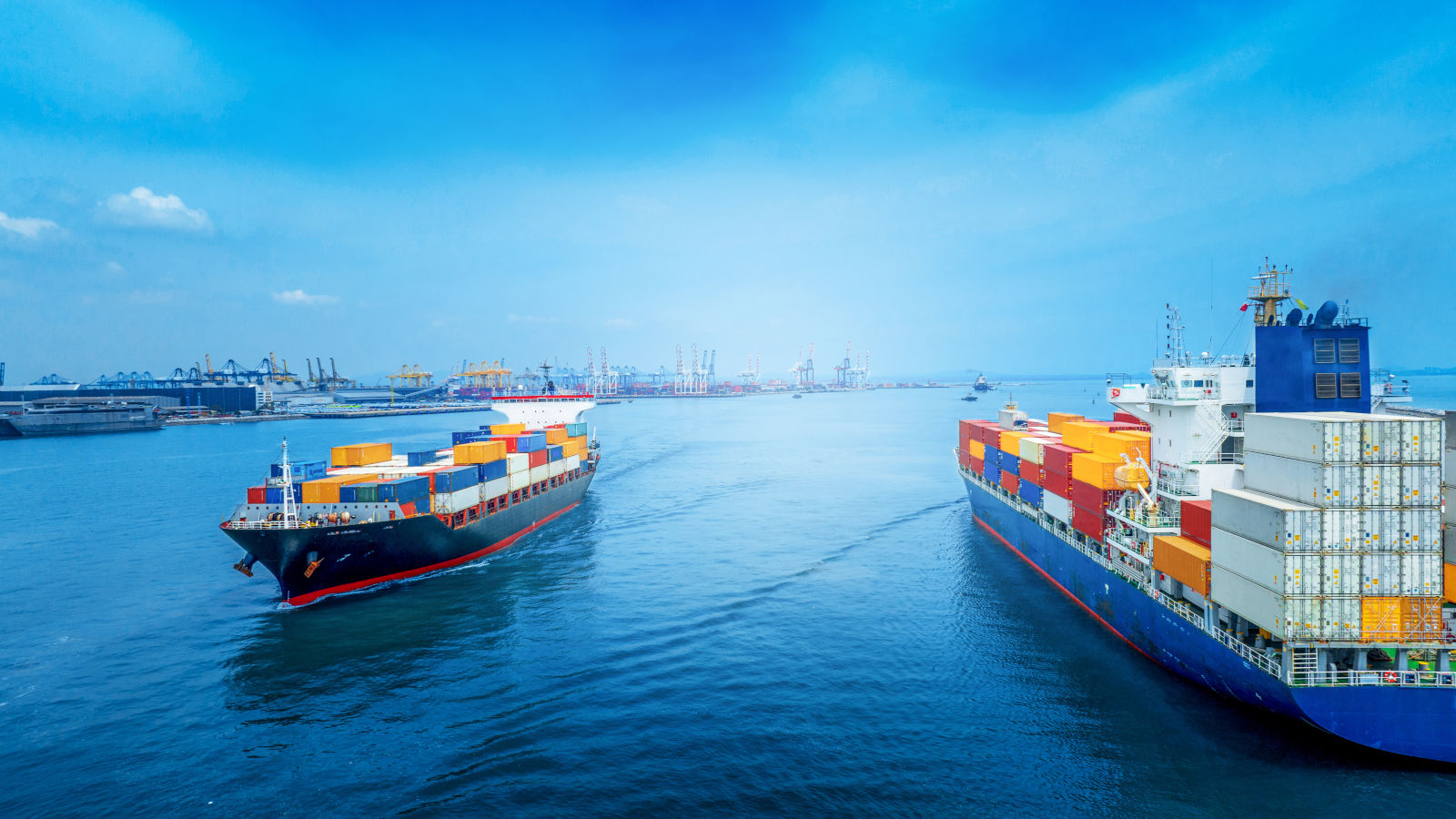
© Adobe Stock / GreenOak
Global Logistics Networks: “The Whole Construct Stood on Feet of Clay”
Rude awakening in production and logistics: supply chains are disrupted, and supplies are lacking across the board. Logistics expert Professor Herbert Kotzab knows why.
The global division of labor was cost-effective and worked – but only as long as there were no interruptions from a global pandemic or a European war. The current situation, however, tells a different story, as Professor Herbert Kotzab explains. A lecturer at the University of Bremen since 2011, he is also Chair of General Business Administration and Logistics Management in the Faculty of Business Studies and Economics.
Professor Kotzab, the world of logistics has obviously been turned upside down. Supply chains are broken. How could this happen?
Herbert Kotzab: It’s not logistics, but rather production that has a problem here. Since manual production in Europe is very expensive, it was gradually outsourced to countries with cost advantages – first to Eastern Europe and later to Asia. This worked well for a long time, very well in fact. In addition, transportation was comparatively cheap because there was excess capacity. Logistics companies undercut each other on freight prices. As a result, many companies in Europe outsourced everything to the Far East.
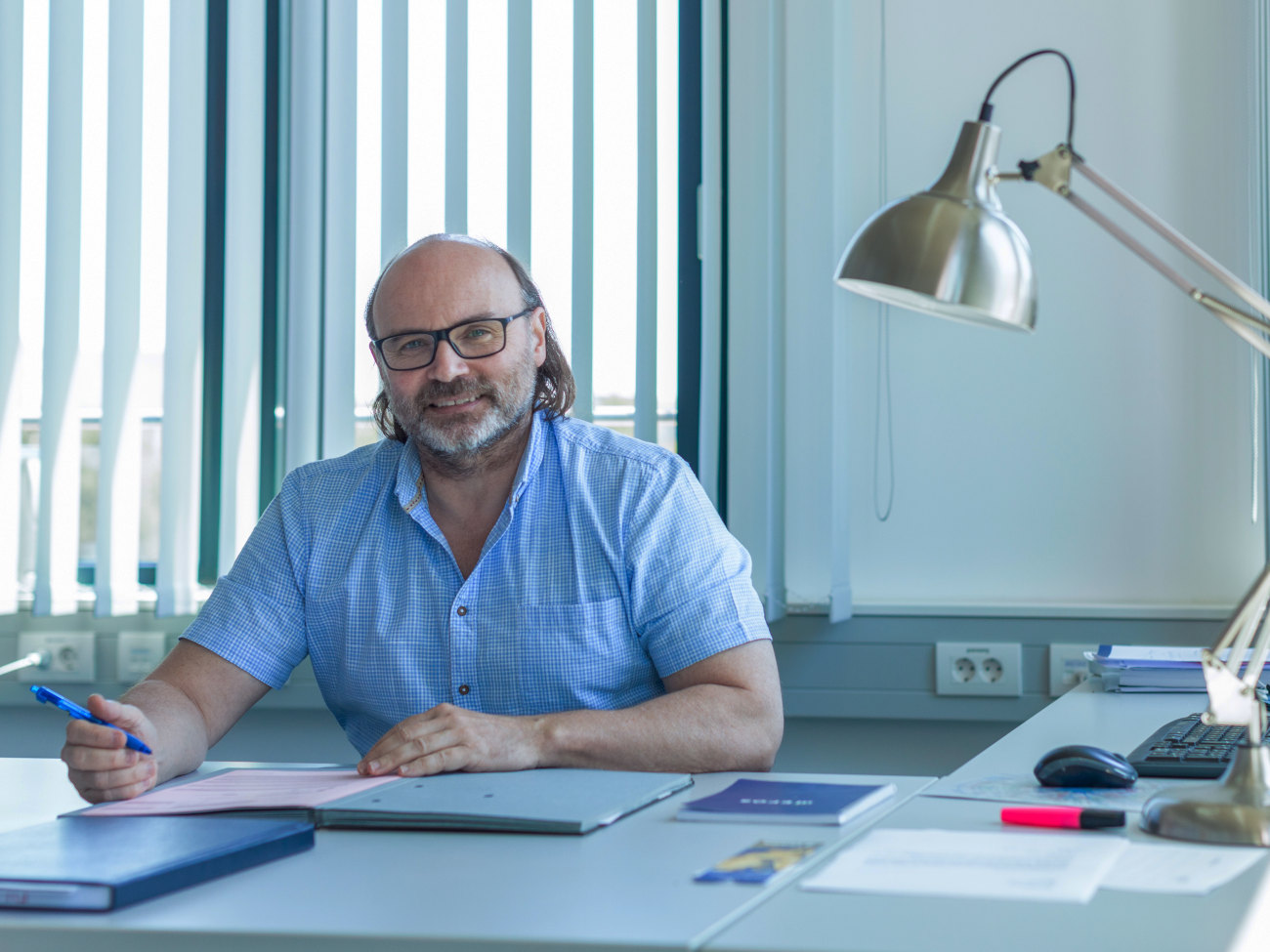
© Matej Meza / Universität Bremen
One of the consequences being previously functioning global logistics networks?
Exactly. Everything was moving along nicely, and we all thought it would carry on like this forever. No one was seriously prepared for incidents of any kind. Then came the unparalleled impact of COVID-19, and one quickly realized that the whole construct was built on feet of clay. There is no safety net. There have been erupting volcanoes that have disrupted air traffic, tsunamis, and even the occasional unusually heavy snowfall – but against COVID-19, these events were merely a slight hiccup. The coronavirus put the brakes on the system – it went from 100 to zero in a very short span of time. And because many companies no longer maintained warehouses, shortages quickly occurred in many areas.
Ship-tracking websites first showed thick clusters off Chinese ports, but now this cluster of container freighters is being seen off European ports. How serious is the situation?
The problem is that these ships don’t drive around like cabs, they move like trains. In other words, they travel according to a timetable. But if, for example, the port in China closes down – i.e., the train station cannot be accessed – it creates a traffic jam, and the timetable becomes obsolete. Even if it things start moving again at some point, space is limited, after all, and the wharves can only accommodate a certain number of ships. In China, this issue is slowly resolving itself, but the congestion has now moved to European shores.
“Transportation costs are rising rapidly, making warehouses a cheaper option once again.” Professor Herbert Kotzab
Do supply chain disruptions just mean that urgently needed goods or even intermediate products simply arrive a bit late – or has a serious threat emerged?
What constitutes a threat? All in all, the logistics industry did a first-class job. There was no breakdown in that sense during the entire period. In the short term, of course, there is a problem because of the way production is designed at the moment. This cannot be changed from one day to the next. For example: In March 2020, during the first coronavirus phase, the automotive industry sharply scaled down its chip demand. So the chip manufacturers have massively cut down their production. Then demand picked up again – but ramping up production again takes time. It’s a manageable segment, with perhaps ten chip factories in the entire world. There was a fire at an American plant, and the Japanese plant was destroyed by an earthquake. So that added to the challenge. And the number of chips required is increasing rapidly every year. There are many similar examples from other industries. So as you can see, logistics is not the overriding problem that is currently making supply so difficult.
So in summary, all’s well in the world of logistics?
Not at all. Because two completely different sectors are currently facing immense problems: in supplying poorer nations with wheat and in energy. Energy for logistics and energy for production was always considered a “given” and was always sufficiently available. And now there’s suddenly this rude awakening. My students are always amazed when I tell them that there was more globalization before the First World War than there is today. But now, unlike back then, globalization is becoming really tangible, a consequence of media potentiation, of course. As far as energy is concerned, we made the big mistake of never asking: What actually happens if it no longer reaches us – because energy logistics doesn’t work, or to put it crudely, because suppliers shut off the gas valve?
Do we need to rethink our disruptive value and supply chains now? Or to put it another way: Will cheap parts soon cost more but be more reliably available from the EU countries instead of from China?
There were times when a lot of things were produced here on-site. Then, in a decades-long process, came the international division of labor and the import of raw materials and intermediate products. Now, based on current disruptions, you could say yes: we are producing more here on-site again. But then we are faced with the next problem – we don’t have people who can do the job, and we can’t teach it to people, because in some cases, we’ve completely done away with the vocational training for it. Knowledge has been lost. So we don’t have enough people with the required expertise or enough basic support staff. There’s staff shortages everywhere in almost all industries.
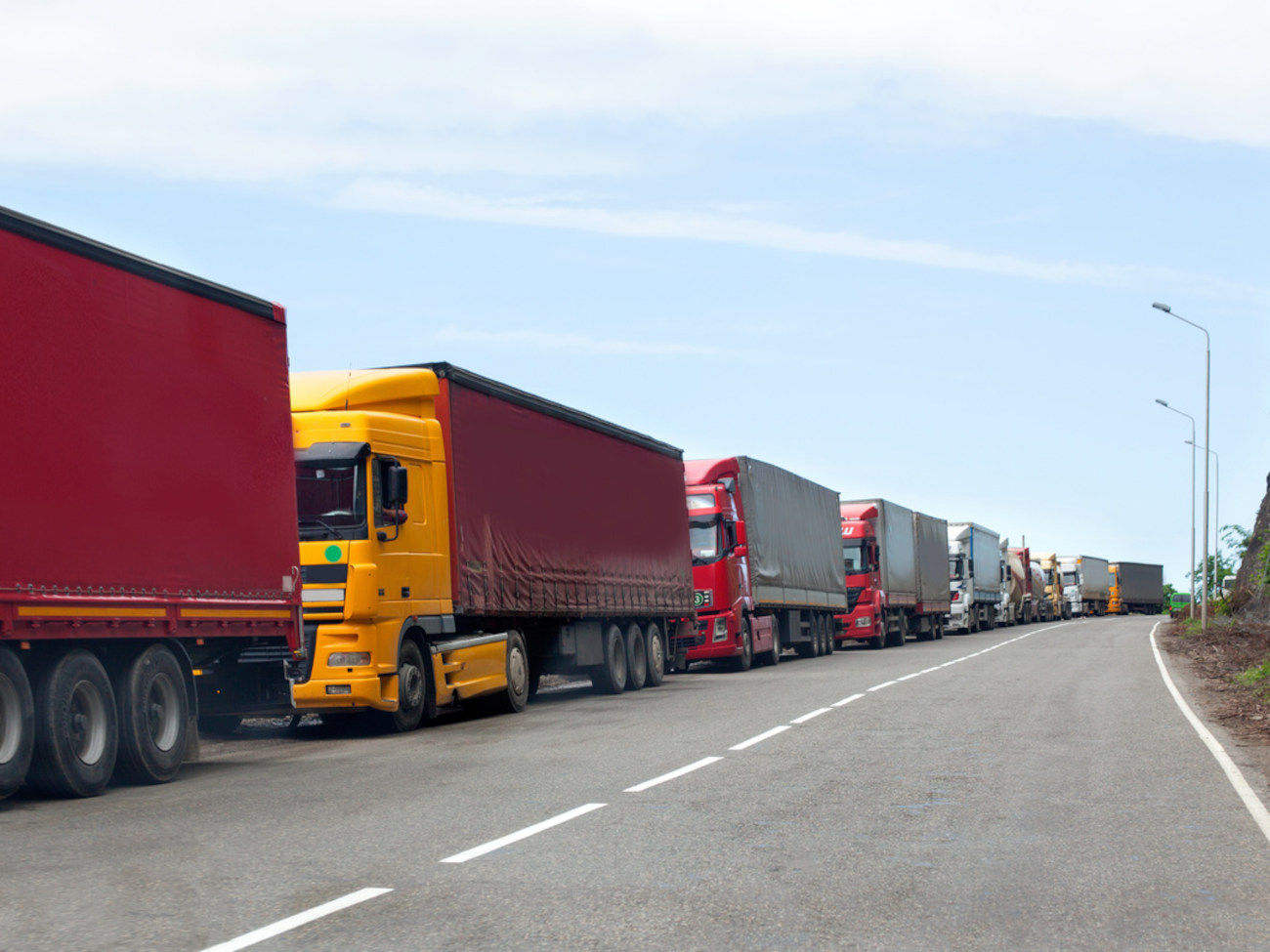
© Adobe Stock / Vera NewSib
One of many examples: Automobile manufacturers have perfected the “just in time” philosophy in recent decades. Parts for car production sometimes arrived at the factory just hours before they were to be used. Will the industry now have to once again build large warehouses on premises?
The overall understanding of “just in time” is not synonymous with the “just in time” philosophy of logistics. “Just in time” means knowing 100 percent what is needed at a specific time in a specific place – without changing anything. Something like this needs comprehensive planning and consistency. But we believe “just in time” would be a way to deal with fluctuations. This is false. In Europe, “just in time” often works because usually the suppliers’ plants are close to the production site. But in Japan, where Toyota invented this concept, sometimes three trucks would set off with parts at once – so that at least one would arrive on time. We in logistics research have long said: It makes perfect sense to invest in warehousing and storage capacity again. Transport costs are rising rapidly, so a warehouse can now be cheaper option again.
You teach and conduct research on General Business Administration and Logistics Management. What are you and your staff particularly interested in?
Personally, I’m interested in what happens in a grocery store – particularly on the sales floor, in the stockroom, what happens on the way between the central warehouse and the stockroom, and – if we look at e-commerce – how the delivery of the goods ordered online is made to the recipient. Another focus is digitization in freight transport, especially rail freight. We are making a research contribution here to make rail freight transport more attractive against the backdrop of climate change.