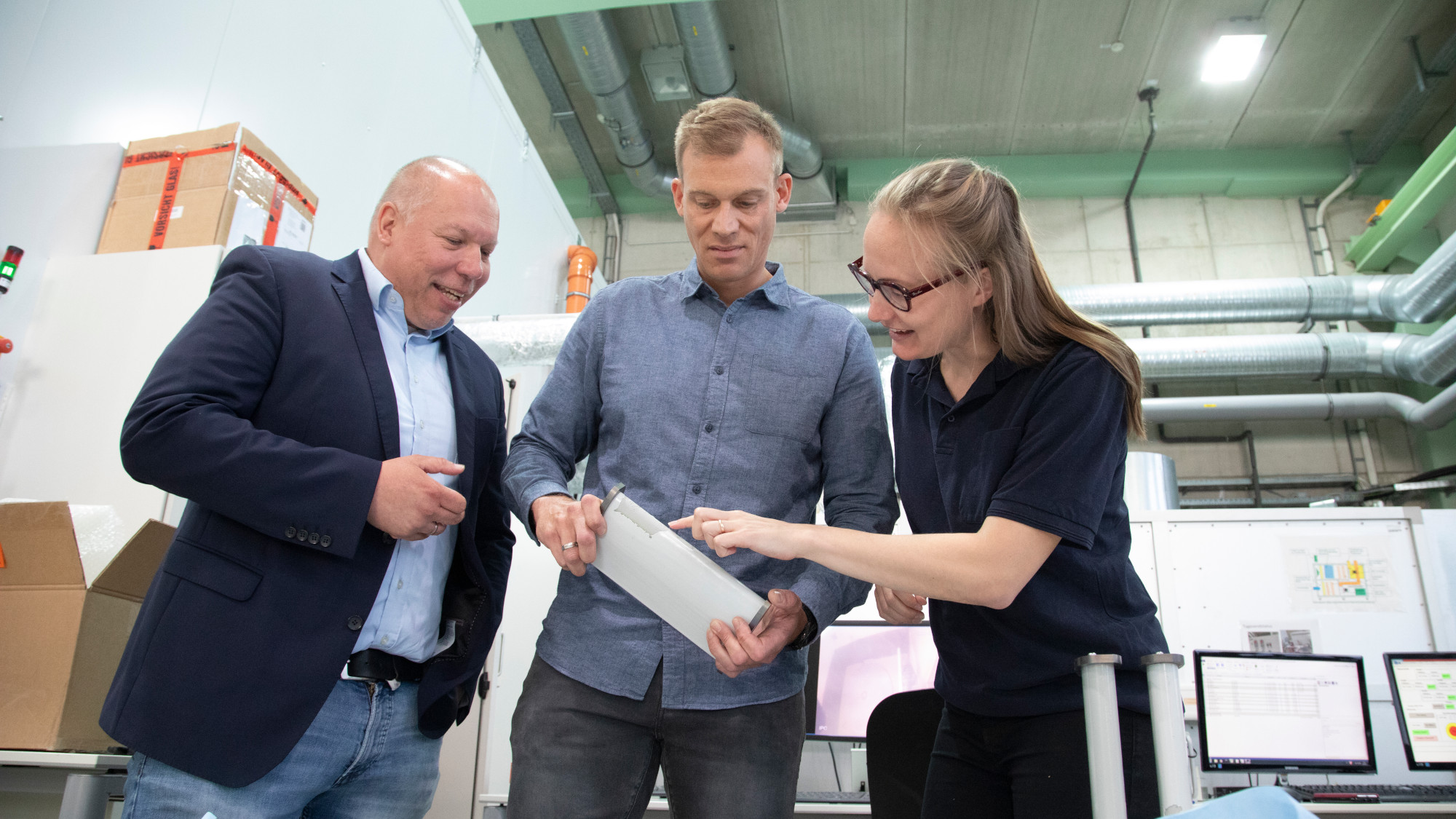
© Jens Lehmkühler
Rain Protection for Rotor Blades
Researchers at the Fraunhofer Institutes IFAM and IWES are making rotor blades more efficient
Small drops, big impact: Over time, rain can damage the surfaces of rotor blades. This reduces the efficiency and profitability of wind turbines, especially at sea. Researchers from institutions of the U Bremen Research Alliance are developing repair solutions to extend the service life of rotor blades.
Picture a large shower cubicle and you are not far off the test bench at the Fraunhofer Institute for Wind Energy Systems IWES in Bremerhaven. The only difference is that the water comes from more than 1,300 needle-shaped nozzles instead of a shower head. The floor of the test stand is fitted with a movable plate which, when rotating, can reach speeds of up to 550 kilometers per hour. Special test objects can be attached to it to represent the rotor blades during the tests. The water droplets hit the surface as they would in nature. The rain intensity is adjustable. A laser-based inspection system automatically scans the surface and documents the smallest changes to determine the effects of the rain drops.
The rain erosion test bench at IWES uses time-lapse technology to simulate the stresses to which the surfaces of rotor blades are subjected during operation. And these are considerable, especially at the leading edges and blade tips. The rotor blade tips rotate at a speed of up to 350 kilometers per hour. The drops hit the surfaces with great force, roughening them, while the sun’s rays and the salts in the sea add to the wear and tear. As the material fatigues, erosion damage can impair the blade’s aerodynamics by increasing the surface roughness and thus making the turbine less effective, even with minimal material abrasion.
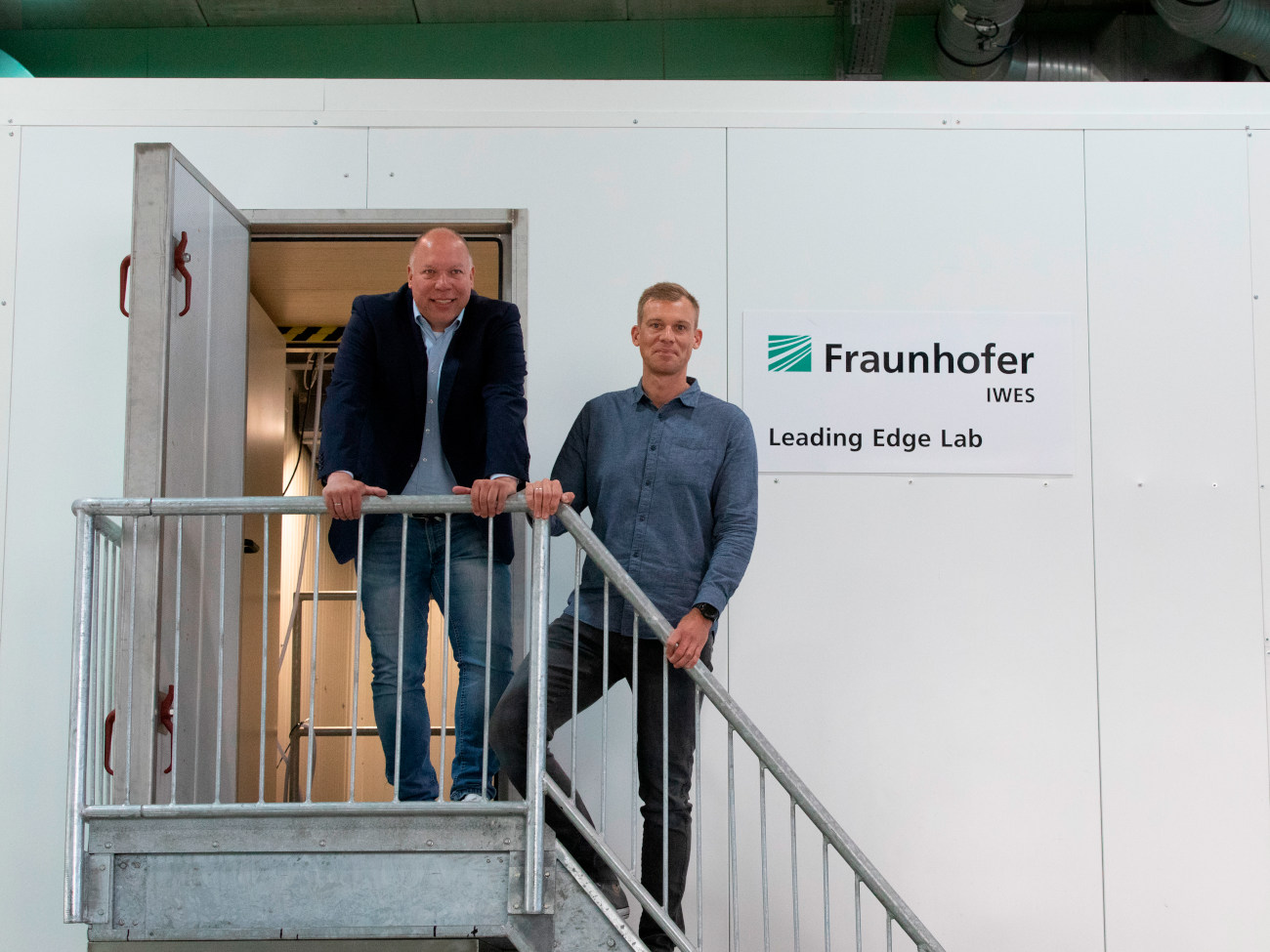
© Jens Lehmkühler
“Yield losses can be in the low single-digit percentage range as the damage progresses,” reports Stefan Krause, technical manager of the Materials Laboratory at IWES. With 1,566 wind turbines in operation in the North and Baltic Seas at the end of 2023, and offshore capacity alone expected to triple by 2030, the yield losses are anything but negligible, especially as it is not only the reduced capacity that poses a challenge.
“Developing repair solutions that are reliable, durable, and also easily implemented is extremely important for the performance and cost-effectiveness of offshore turbines” Sascha Buchbach
If the erosion is not repaired and continues to progress, in individual cases, the surface can crack. This can allow water to penetrate the rotor blades and change the weight distribution, which can ultimately lead to imbalances and cause vibrations. The target life of a turbine of around 20 years is jeopardized and repairs become necessary. In the worst case, the blades have to be removed for an overhaul on land. These maintenance operations are expensive, especially at sea. Ships have to be chartered and industrial climbers hired. Each day of repair costs around 20,000 euros. This type of damage occurs on land as well, but is easier to repair.
“Developing repair solutions that are reliable, durable, and also easily implemented is extremely important for the performance and cost-effectiveness of offshore turbines,” states Sascha Buchbach, working group manager for paint testing and application technology at the Fraunhofer Institute for Manufacturing Technology and Advanced Materials IFAM in Bremen, which, like the Fraunhofer IWES, is a member of the U Bremen Research Alliance.
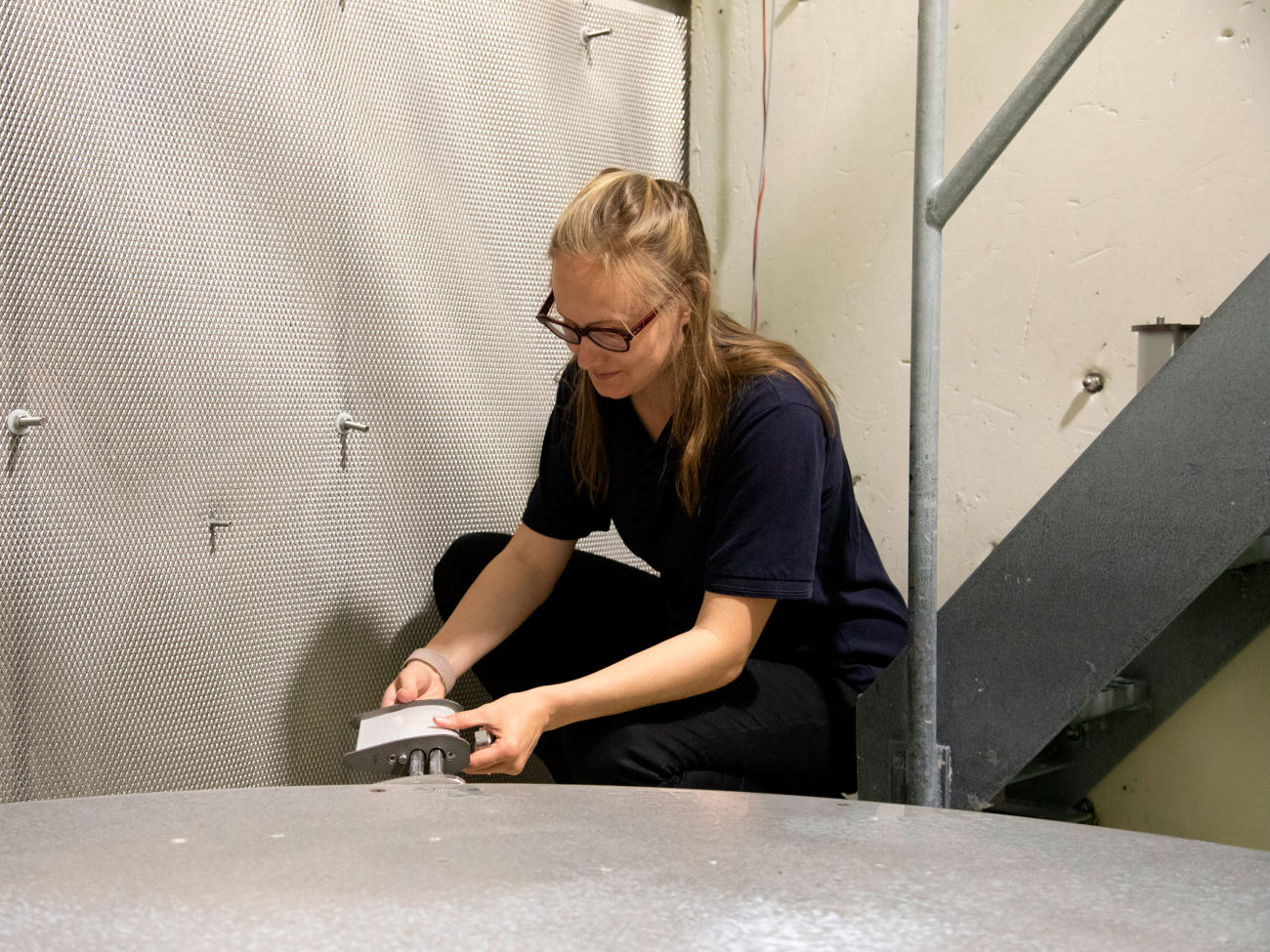
© Jens Lehmkühler
The aim of MARiLEP – a joint project for material and repair innovations for offshore leading-edge protection systems – is to develop new repair methods and products to better protect the leading edges of rotor blades. The project is coordinated by Fraunhofer IFAM and will receive around 1.6 million euros in funding from the German Federal Ministry of Economic Affairs and Climate Action (BMWi).
Different systems are used to protect the leading edges of the blades. Some manufacturers use paint, others foils. Some coatings are elastic and allow raindrops to bounce off; others are hard so that they break the drops. “We will also develop metallic caps that include lightning protection,” emphasizes Buchbach. Self-repairing paints, which contain micro-encapsulated ingredients within a coating, are to be used as well. In the event of damage, the microcapsules rupture and release a liquid that hardens the crack. The solutions should be long lasting, and easy to implement without being limited by a small application window or ideal weather conditions.
The first step, however, is to better understand the damage mechanisms, analyze the current situation, and create a damage register. To do this, the test conditions must be as close to real life as possible. In addition to Stefan Krause, the IWES research assistant Cate Lester is responsible for damage analysis in the materials testing laboratory. The American came to IWES after completing her master’s degree in wind energy at the Technical University of Copenhagen. Why did she come to Bremerhaven? “Because this is a good place for applied research into wind energy! The development of green energy is important to me.”
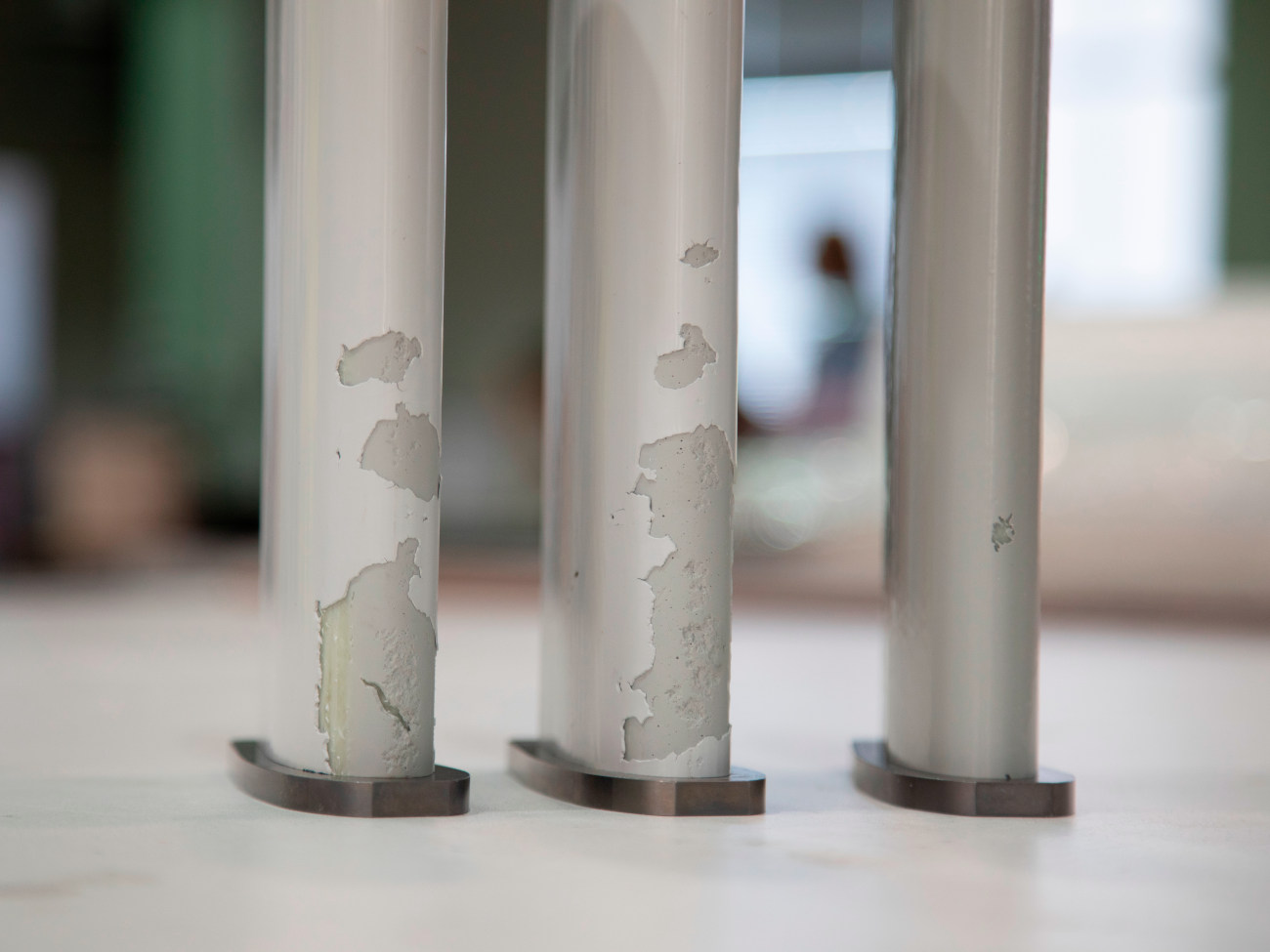
© Jens Lehmkühler
The rain erosion test bench is just one of several test facilities at IWES. On the same site, at the rotor blade test facility, which began operations in 2023, rotor blades with a length of more than 115 meters undergo a series of tests before they go into large-scale production. Rotor blades are crucial for the performance, reliability, and cost efficiency of a wind turbine. Investment in their development and protection is essential, and research on them is an important building block on the road to a carbon neutral future. At the same time, it strengthens the location Bremerhaven, which has developed into a national research hub for wind energy and attracts scientists who are committed to developing this technology. Among them are not only Cate Lester, but also Stefan Krause from Oldenburg. “Wind energy,” states the measurement engineer, “is also interesting from a technical point of view.”
“We complement each other very well.” Sascha Buchbach
At the Fraunhofer IFAM, the basis for the use of new materials in wind energy is created in its numerous materials laboratories. Here, material properties are determined, thermal material behavior is analyzed, and aging mechanisms are investigated. The knowledge gained is incorporated into the damage analysis and is particularly valuable for the development of future materials. The two institutes, Fraunhofer IWES and Fraunhofer IFAM, work together on projects beyond MARiLEP. While IFAM specializes in developing new materials, IWES’ expertise lies in the development and validation of test procedures. “We complement each other very well,” emphasizes engineer Buchbach, who is celebrating his 25th anniversary at IFAM.
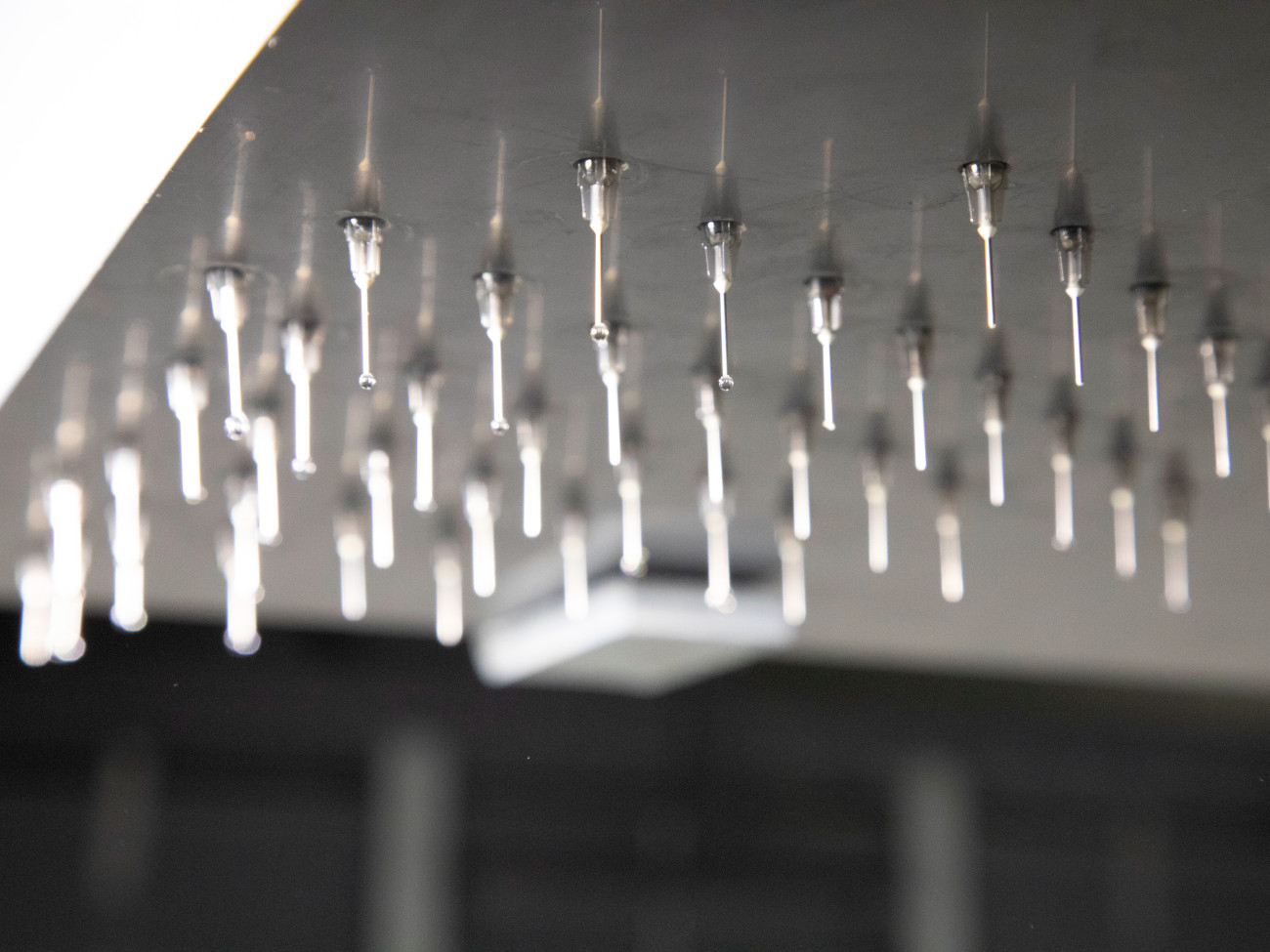
© Jens Lehmkühler
In addition to the scientists, the project consortium also consists of manufacturers of coating systems for erosion protection, and wind farm repair specialists. “What I find so exciting about the project is that we are developing new materials and repair concepts with our partners that are ready for serial production,” emphasizes Buchbach. “Ultimately, the aim is to enable wind turbines to operate for longer and reduce maintenance costs.” Three products – a coating, a foil system, and a metallic protective cap – are to be launched as part of MARiLEP. These could be released in 2026, and the project is funded until then.
One of the challenges with the repair solutions is their field of application: If the air is too cold, the wind too strong, or the humidity too high, repairs are not possible. The new technologies will significantly extend the time until repairs are needed. Still, the specialists needed to carry out these repairs offshore are scarce and expensive. To solve this problem, Buchbach already has a future scenario in mind: drones! These could inspect the rotor blades, detect damage, and repair them by themselves. “But a lot of research needs to be done before that would be possible.”
Offshore Drones
With the expansion of wind turbines off the coasts, there is an equally growing market for inspection and maintenance work. Fraunhofer IFAM is responding to this growing demand with the establishment of its “Offshore Drone Campus Cuxhaven” (ODCC), a test and development infrastructure for unmanned aircraft systems. The new location will serve as a place for further developing offshore drones with the help of scientific and industrial partners. Their research focuses on the safe and efficient use of drones for offshore maintenance, inspection, repair, and surveying, as well as the development of new ideas to protect drone engines and materials for the demanding use in offshore conditions.
Der Artikel stammt aus Impact- Dem Wissenschafts-Magazin der U Bremen Research Alliance
In U Bremen Research Alliance kooperieren die Universität Bremen und zwölf Institute der bundländerfinanzierten außeruniversitären Forschung. Die Zusammenarbeit erstreckt sich über vier Wissenschaftsschwerpunkte und somit „Von der Tiefsee bis ins Weltall“. Das Wissenschafts-Magazin Impact gibt zweimal im Jahr spannende Einblicke in das Wirken der kooperativen Forschung in Bremen.