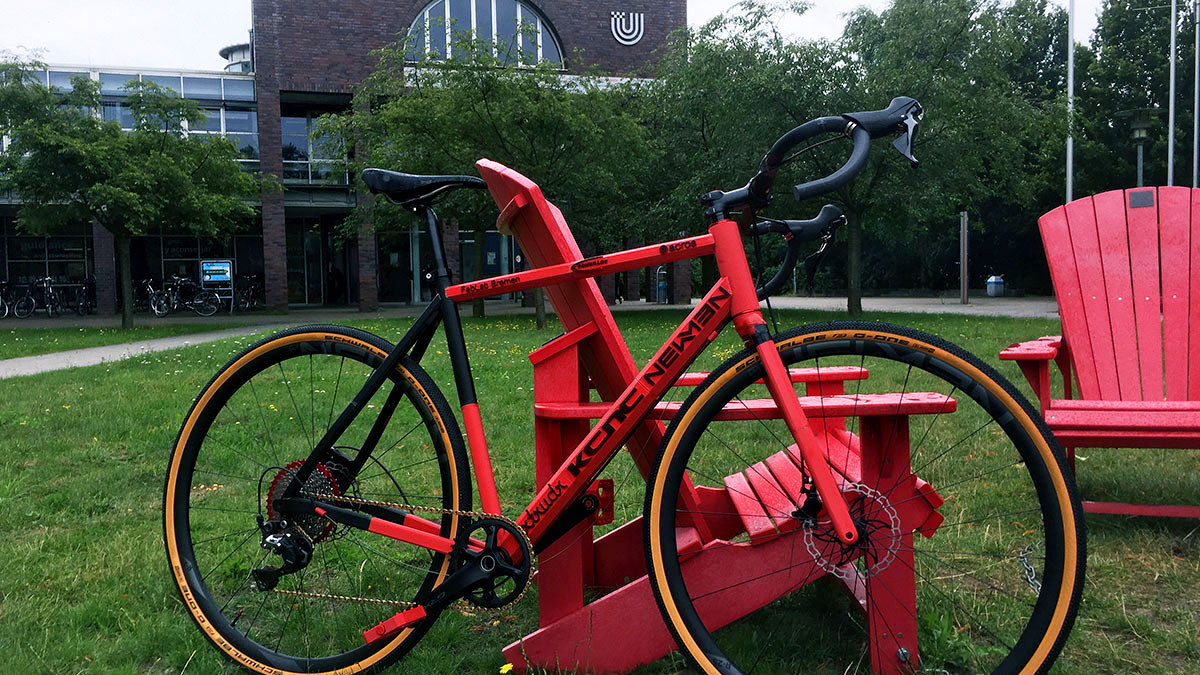
© Till Kolligs
Das gedruckte Fahrrad
Studierende produzieren ein Fahrrad mit einem 3D-Drucker
Wie sieht die Zukunft des Fahrrads aus? Wenn man die Gruppe von Studierenden um Till Kolligs fragt, lautet die Antwort: Es muss leicht, nachhaltig und zugleich erschwinglich sein. Im Bremer FabLab entwickelten sie nicht nur ihren Entwurf, sondern druckten das Fahrrad mit einem handelsüblichen 3D-Drucker.
Die neuen Möglichkeiten, die der 3D-Druck bietet, faszinieren Till Kolligs und seinen Mitbewohner schon seit langem. Gemeinsam mit drei weiteren Studierenden der Universität Bremen machten sie sich mehr als ein halbes Jahr lang Gedanken über die Zukunft des Fahrradbaus. Wie produziert man ein leichtes, nachhaltiges und dennoch bezahlbares Fahrrad? Und wie kann man es ohne Stahl, Aluminium oder Carbon produzieren?
Ein leichtes, ergonomisches Fahrrad für die Stadt
Für ihre Planungen sahen sich die Studierenden aus den Bereichen Soziologie, Digitale Medien und Produktionstechnik zunächst einmal die Stadt genauer an. „Bremen ist eine sehr fahrradfreundliche Stadt“, stellt Till Kolligs fest. „Der hohe Radverkehrsanteil ist auch politisch gewollt und gefördert“. Dennoch gäbe es insbesondere in der Innenstadt Herausforderungen für Radbesitzer. Es mangele an sicheren Abstellorten, sodass die Bewohnerinnen und Bewohner ihre Räder teilweise mehrfach täglich Treppen hinab- und wieder hinauftrügen. Außerdem seien viele Räder in ihrer Ergonomie nicht genug an die Fahrerin oder den Fahrer angepasst.
„Uns sollte also die Quadratur des Kreises gelingen: Ein Fahrrad zu entwerfen, dass individualisierbar ist hinsichtlich seiner Geometrie, leicht ist, sodass es auch gut getragen werden kann, und obendrein noch bezahlbar und nachhaltig ist“, so Kolligs. „Insbesondere der Nachhaltigkeitsaspekt sollte nicht zu kurz kommen, benötigen herkömmliche Materialien wie Stahl und Aluminium sehr viel Energie bei der Herstellung, und bedrohen allein bei der Gewinnung den Bestand von Regenwäldern. Die Technologie die verspricht diesen Wunsch möglich zu machen, ist der 3D-Druck.“
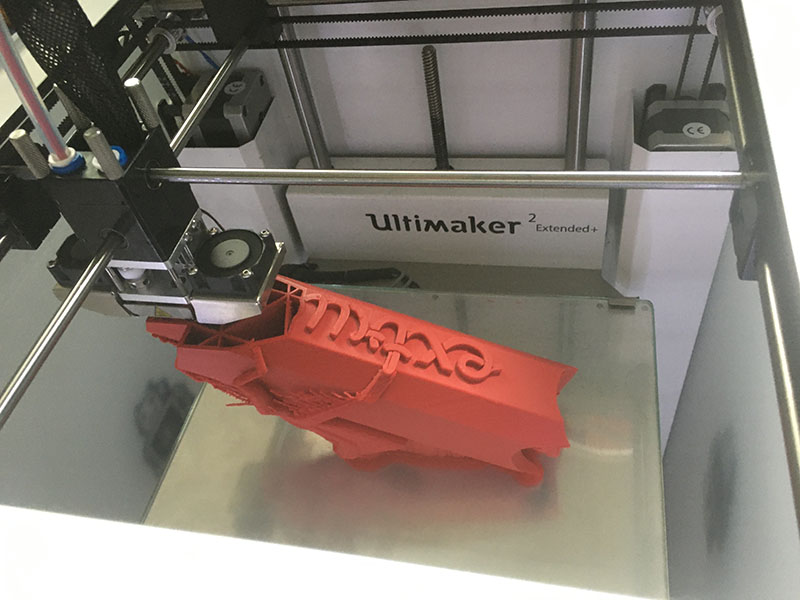
© Till Kolligs
Im nächsten Schritt ging es an die konkrete Planung und Materialrecherche. Schnell war klar: Nicht alle Bauteile können gedruckt werden. Unter anderem die Reifen, Kette und Bremsen kamen von außerhalb. „Die Produktion dieser Bauteile wären nochmal ganz eigenständige Projekte“, verrät Kolligs. „Wir haben uns daher zunächst auf die Produktion des Rahmens konzentriert.“ Damit das Fahrrad am Ende trotzdem fahrtüchtig ist wurde die Gruppe von mehreren Herstellern unterstützt, wie etwa NEWMEN die einen ihrer leichten Laufradsätze zur Verfügung stellten, KCNC die Kassette, Kette und Scheibenbremsen sponsorten, als auch von Acros und Schwalbe.
Die Anforderungen an das Material waren hoch: Ein Fahrrad muss stabil sein und hohen Belastungen standhalten. Die Gruppe kam letztlich auf den Filamenthersteller Extrudr in Österreich, der ihnen das eigens entwickelte Material „GreenTec Pro“ zur Verfügung stellte. „Das Material weist eine gute Biegefestigkeit auf und hält auch äußeren Schlageinwirkungen stand. Zudem ist es unter bestimmten Bedingungen biologisch abbaubar und wird nicht auf Erdölbasis hergestellt – das war uns sehr wichtig“, verrät Kolligs.
Eine Herausforderung war der auch die Planung des Drucks: Im FabLab an der Universität Bremen konnte die Gruppe einen Drucker mit hoher Genauigkeit nutzen, der jedoch nur einen Bauraum von 223 mal 223 Millimetern aufweist. Somit musste der Rahmen in mehreren Teilen gedruckt werden. Zudem musste das Design kompatibel zu jenen Teilen sein, die nicht gedruckt werden konnten.
Wie druckt man einen Rahmen?
Das zu druckende Fahrrad sollte ein Gravelbike sein, ein geländetaugliches Modell mit einem diamantförmigen Rahmen. Nach der Modellierung am Computer folgten die ersten Testdrucke und ein Zugtest, um die Druckparameter festzulegen. „Danach gab es viele Fehldrucke und Verbesserungen“, erzählt Kolligs. „Bis zum finalen Modell verbrauchten wir fast das gesamte Material, das uns zur Verfügung stand.“ Nach dem letzten Druck stand das Team vor der größten Herausforderung: Die Verbindung der einzelnen Teile zu einem Rahmen.
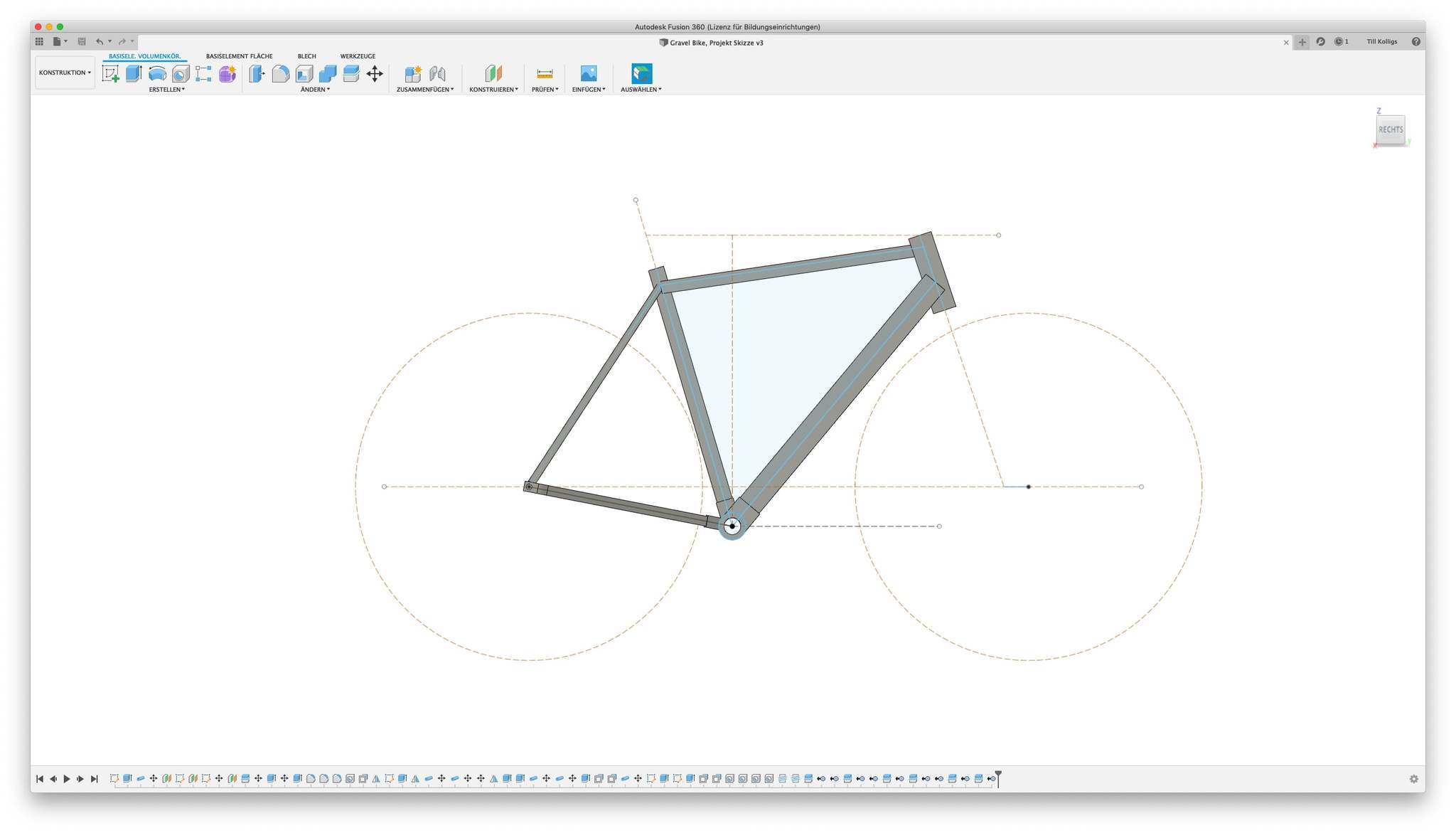
© Till Kolligs
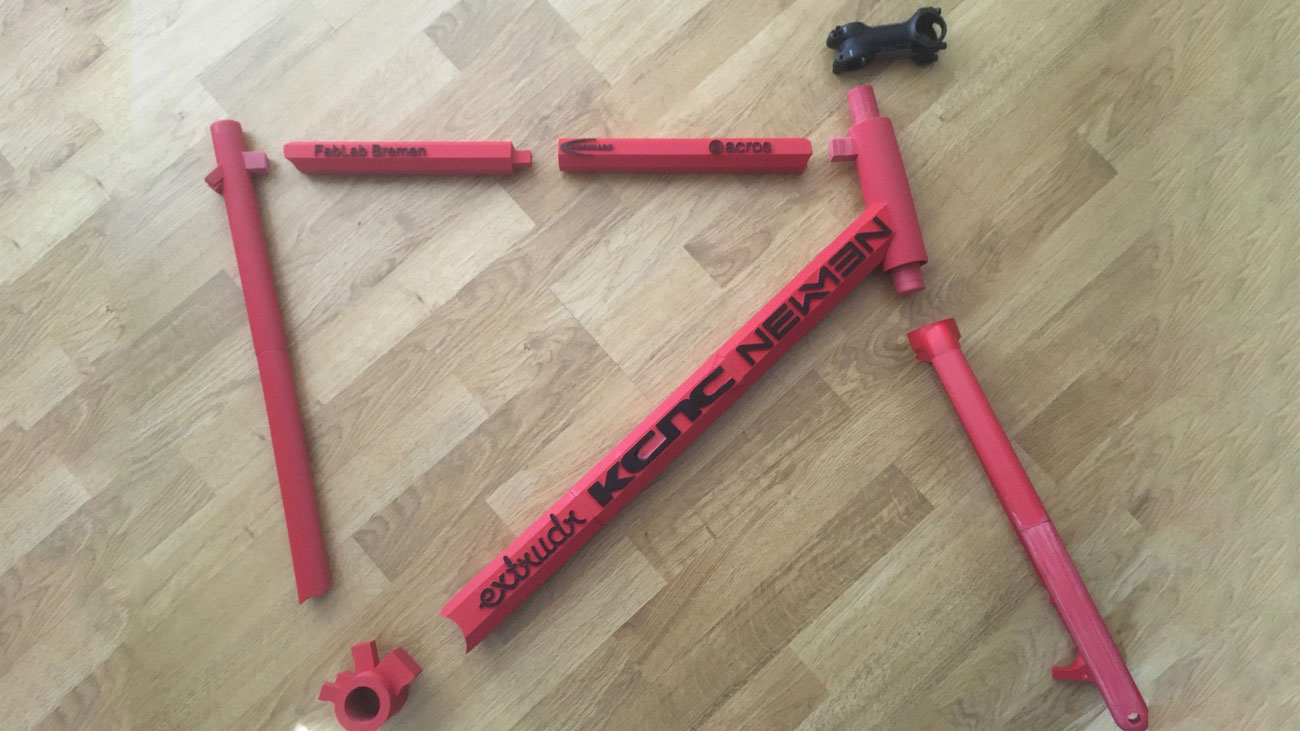
© Till Kolligs
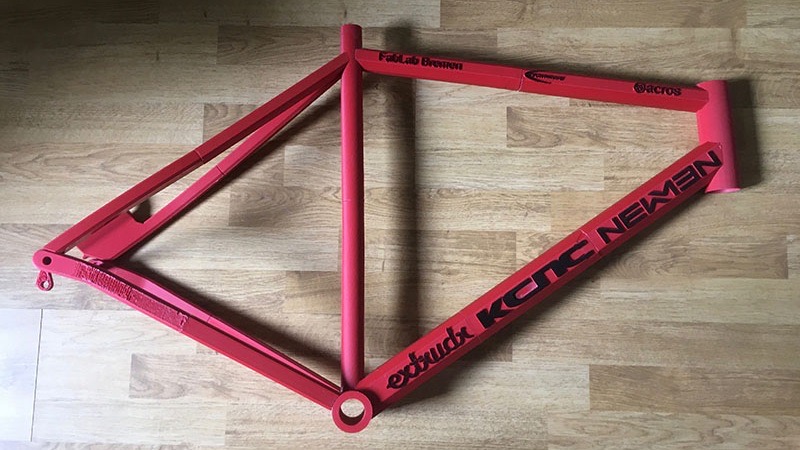
© Till Kolligs
„Optimal wäre es gewesen, die gedruckten Teile mit einem Hoch-Frequenz-Schweißverfahren zu verbinden“, so Kolligs. „Doch dafür hatten wir keine Maschine. Also experimentierten wir mit Steckverbindungen und PVC-Kleber. Letztendlich arbeiteten wir dann jedoch mit Zwei-Komponenten-Epoxidharzkleber. Epoxidharzkleber ist unter bestimmten Bedingungen einer der stärksten Kleber, die es gibt, für unseren Zweck jedoch leider nicht perfekt. Ähnlich zu einem Aluminium-Rahmen sind die Verbindungen die wesentlichen Schwachpunkte des Rahmens geworden.“
Die erste Probefahrt
Dennoch wurde das Rad fertig: „Aus vielen Gedanken, Schweiß, Frust und Geduld ist letztendlich der finale Rahmen hervorgegangen, auch wenn er nach wie vor ein Prototyp ist. Der Moment, als wir dann jedoch endlich alle Teile an den Rahmen bauen konnten, alles gepasst hat, die Bremsen nicht geschleift haben und man reibungslos schalten konnte, war ein toller Moment“, berichtet Kolligs.
„Die Arbeit hatte sich gelohnt. Obwohl wir den Fokus auf Stabilität und nicht auf Gewicht gelegt haben wog der fertige Rahmen grade einmal 1450 Gramm, die Gabel lediglich 350g. Zudem kann er im Computer leicht auf andere Körpergrößen angepasst werden. Das erste Draufsetzen war ebenfalls ein spannender Moment, doch der Rahmen hielt. Das Problem war weniger der Rahmen an sich, als die Fahrradgabel, die beim ersten Anrollen etwas nachgab. Die Gabel hielt keinem großen Gewicht stand, und brach bei einer Testbremsung an einer Klebestelle, bei der die Belastung am größten war. In einem nächsten Schritt muss die Gabel also in einem Stück mit einem großen Drucker und eventuell auch dicker gedruckt werden.“
Trotzdem ist das Team zufrieden: „Wir haben gezeigt, dass man das Rad durchaus neu erfinden kann“, so Kolligs. Der Prototyp zeige, dass es grundsätzlich möglich ist, belastbare Fahrräder mit dem 3D-Druckverfahren zu bauen. „Auch wenn uns das Projekt viel Zeit gekostet hat, sind wir sehr froh, es begonnen zu haben. Die Universität Bremen und das FabLab haben uns die Möglichkeit gegeben, eine zunächst etwas verrückt klingende Idee in die Realität zu bringen!“
Über das FabLab
Das FabLab (Fabrication Laboratory) ist ein Ort, an dem Schülerinnen und Schüler, Studierende und Lehrkräfte die Möglichkeit haben, mit Technologien und Materialien zu experimentieren und während des Herstellens zu lernen („Learning-by-design“). Es werden unter anderem 3D-Drucker, Vinyl-Plotter und Arduino-Technologie eingesetzt, um den kreativen Umgang mit Technologie zu fördern und diese „be-greifbar“ zu machen. Es wird von der Arbeitsgruppe Digitale Medien in der Bildung (dimeb) im Fachbereich Mathematik/Informatik der Universität Bremen betrieben.