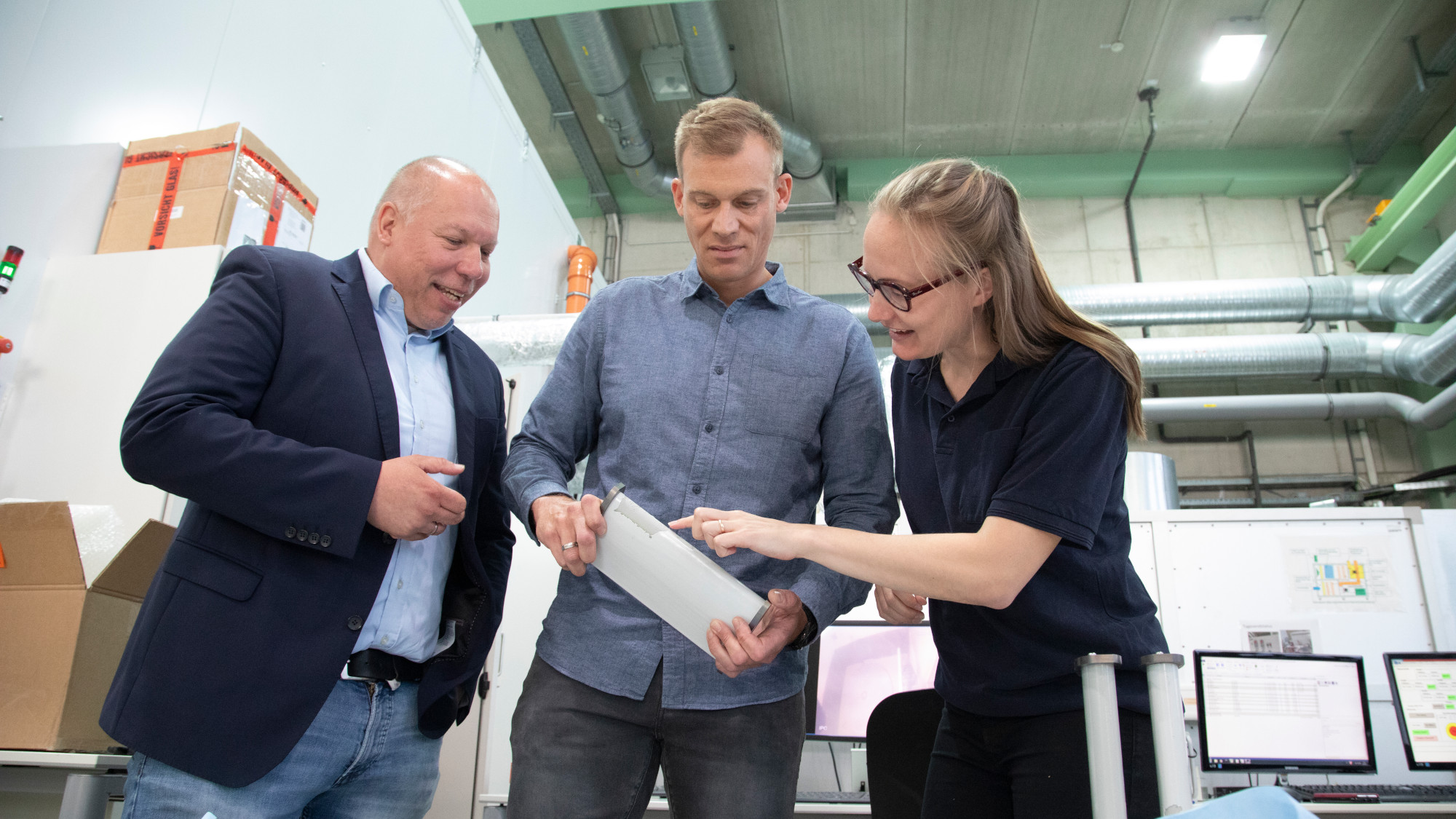
© Jens Lehmkühler
Regenschutz für Rotorblätter
Forschende der Fraunhofer-Institute IFAM und IWES arbeiten daran, Rotorblätter leistungsfähiger zu machen
Kleine Tropfen, große Wirkung: Regen kann auf Dauer die Oberflächen von Rotorblättern beschädigen, die Leistungsfähigkeit und Wirtschaftlichkeit von Windenergieanlagen können sinken, vor allem auf See. Durch die Entwicklung innovativer Reparaturlösungen wollen Wissenschaftler:innen aus Mitgliedseinrichtungen der U Bremen Research Alliance die Lebensdauer der Rotorblätter verlängern.
Man kann sich den Prüfstand im Technikum des Fraunhofer-Instituts für Windenergiesysteme IWES in Bremerhaven wie eine große Duschkammer vorstellen. Nur kommt das Wasser statt aus einem Duschkopf aus mehr als 1.300 nadelförmigen Düsen. Am Boden des Prüfstands ist eine bewegliche Platte befestigt, die beim Rotieren an der äußeren Kante eine Geschwindigkeit von bis zu 550 Stundenkilometern erreichen kann. An ihm können spezielle Prüfkörper befestigt werden, die in den Versuchen für die Rotorblätter stehen. Auf sie treffen, wie in der Natur, die Wassertropfen. Die Intensität des Regens ist regulierbar. Seine Auswirkung ermittelt ein laserbasiertes Inspektionssystem, das automatisch die Oberfläche scannt und kleinste Veränderungen dokumentiert.
Der Regenerosionsprüfstand am IWES simuliert im Zeitraffer die Belastungen, denen die Oberflächen von Rotorblättern im Betrieb ausgesetzt sind. Und diese sind erheblich, insbesondere an den Rotorblattvorderkanten und an den Rotorblattspitzen. Durch die Rotordrehung bewegen sich die Rotorblattspitzen mit einer Geschwindigkeit von bis zu 350 Stundenkilometern. Mit großer Wucht prallen die Tropfen auf die Oberflächen und rauen diese auf, die Sonneneinstrahlung und die Salze auf See tun das Ihrige. Das Material ermüdet, Erosionsschäden können entstehen, die durch die Zunahme der Oberflächenrauheit zu einer Beeinträchtigung der Aerodynamik der Blätter führen und selbst bei minimalem Materialabtrag die Leistung der Anlage reduzieren können.
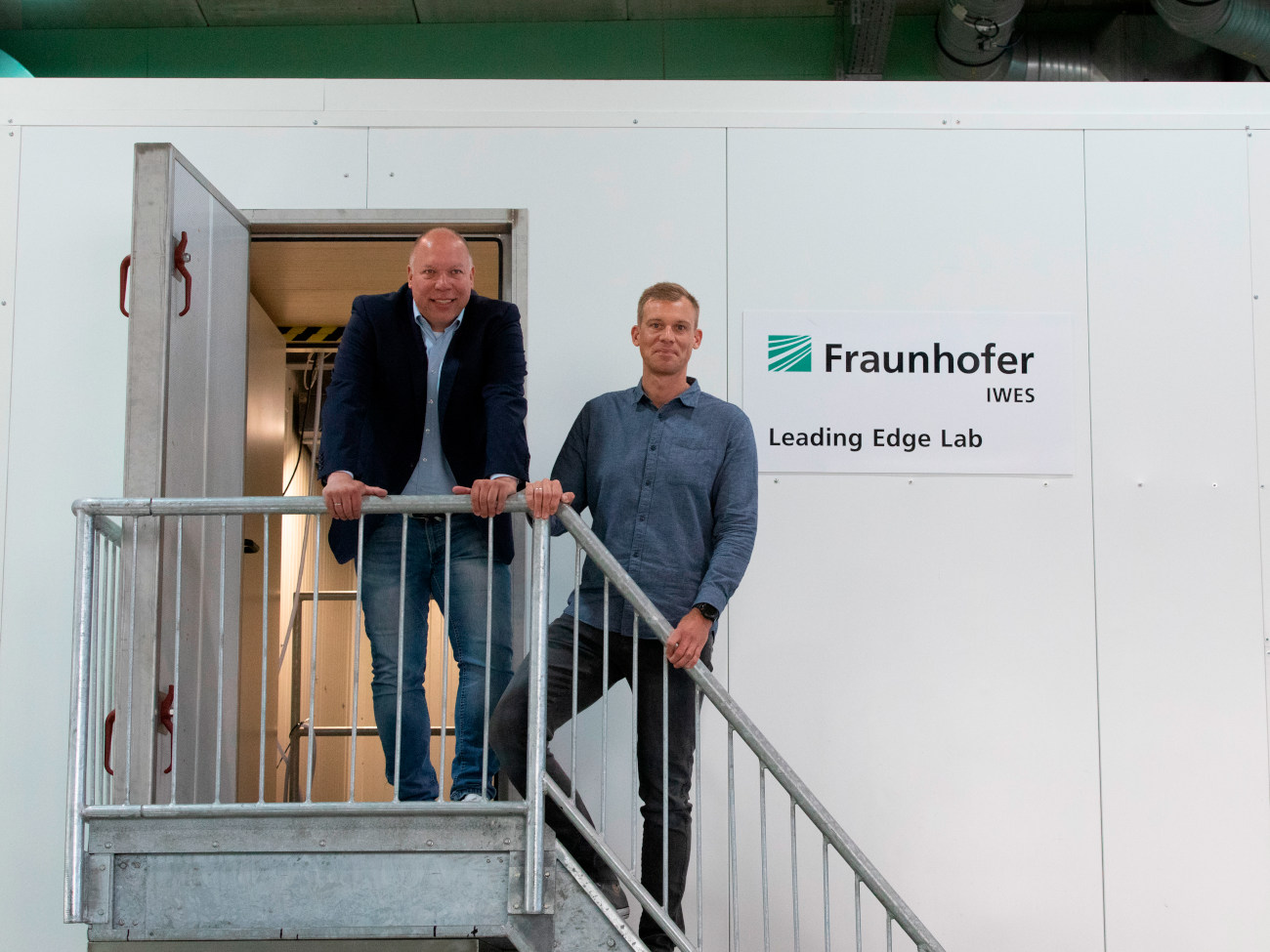
© Jens Lehmkühler
„Die Ertragsverluste können bei fortschreitender Schädigung im niedrigen einstelligen Prozentbereich liegen“, sagt Stefan Krause, Technischer Leiter des Materiallabors am IWES. Angesichts von 1.566 Windenergieanlagen in Nord- und Ostsee, die Ende 2023 in Betrieb gewesen sind, sowie einer angepeilten Verdreifachung allein der Offshore-Leistungen bis 2030 sind die Ertragseinbußen alles andere als unerheblich, zumal der Rückgang der Leistung nicht die einzige Herausforderung ist.
„Die Entwicklung von zuverlässigen, langzeitbeständigen und einfach anzubringenden Reparaturlösungen hat für die Leistungsfähigkeit und Wirtschaftlichkeit der Offshore-Anlagen eine hohe Bedeutung.“ Sascha Buchbach
Wenn die Erosion nicht repariert wird und weiter fortschreitet, kann es in Einzelfällen zu Rissen kommen. Dadurch kann Wasser in die Rotorblätter eindringen und die Gewichtsverteilung verändern. Unwuchten und Vibrationen können die Folge sein. Das Ziel einer Lebensdauer einer Anlage von rund 20 Jahren ist gefährdet, Reparaturen werden nötig. Im schlimmsten Fall müssen die Blätter abgenommen und an Land überarbeitet werden. Diese Wartungseinsätze sind mit einem hohen finanziellen Aufwand verbunden, insbesondere auf See: Schiffe müssen gechartert, Industriekletterer:innen angeheuert werden. Pro Tag kostet ein Reparatureinsatz rund 20.000 Euro. Auch an Land treten diese Schäden auf, sind allerdings einfacher zu reparieren.
„Die Entwicklung von zuverlässigen, langzeitbeständigen und einfach anzubringenden Reparaturlösungen hat für die Leistungsfähigkeit und Wirtschaftlichkeit der Offshore-Anlagen eine hohe Bedeutung“, sagt Sascha Buchbach, Gruppenleiter Lackprüfungen und Anwendungstechnik am Fraunhofer-Institut für Fertigungstechnik und Angewandte Materialforschung IFAM in Bremen, wie das Fraunhofer IWES eine Mitgliedseinrichtung der U Bremen Research Alliance.
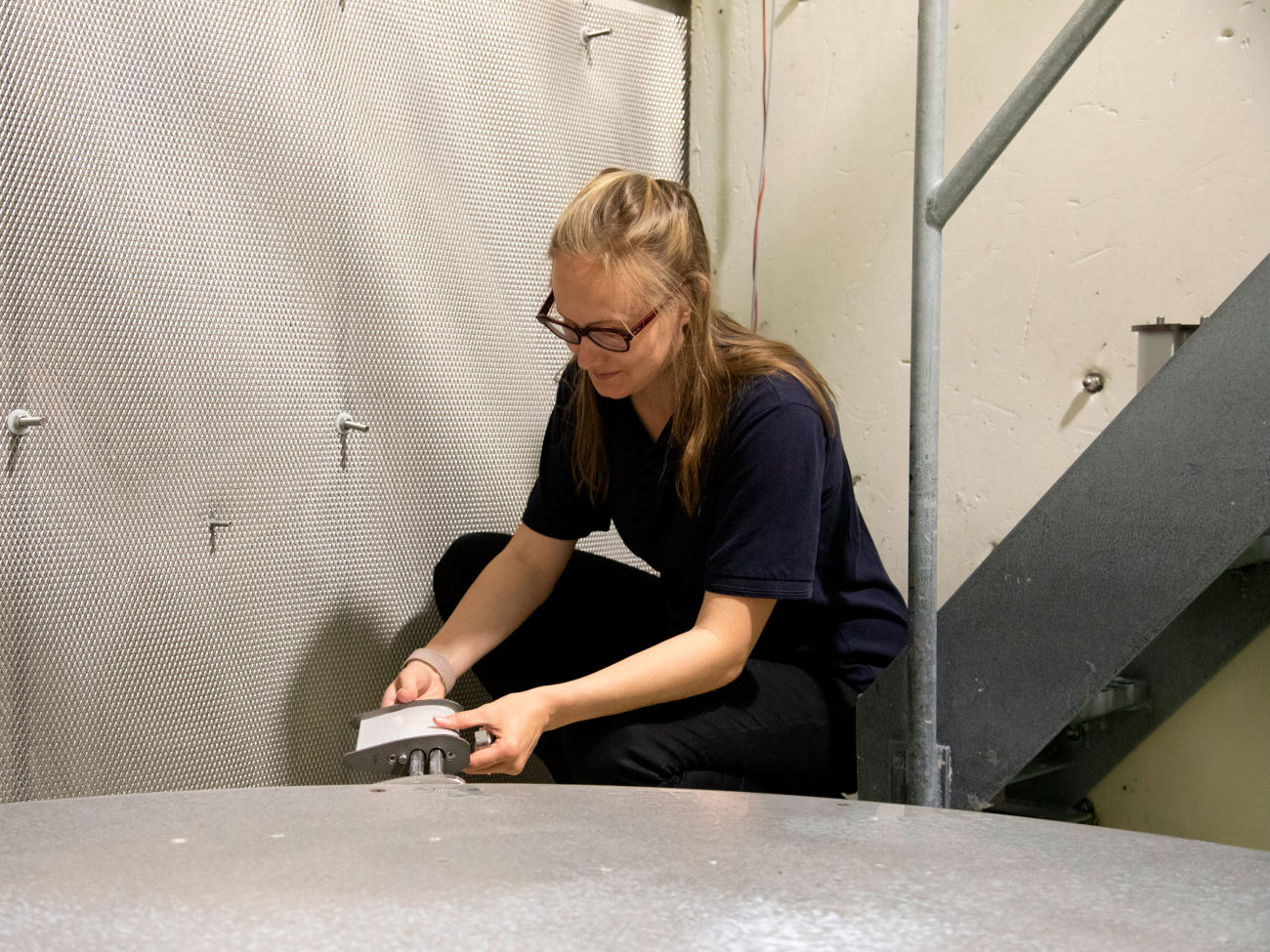
© Jens Lehmkühler
Neue Reparaturkonzepte und Produkte zum besseren Schutz der Blattvorderkanten zu entwickeln, ist das Ziel von MARiLEP, dem „Verbundprojekt für Material und Reparaturinnovationen für Offshore Leading-Edge-Protection Systeme“. Koordiniert vom Fraunhofer IFAM, wird es vom Bundesministerium für Wirtschaft und Klimaschutz (BMWK) mit rund 1,6 Millionen Euro gefördert.
Um die Blattvorderkanten zu schützen, werden unterschiedliche Systeme eingesetzt: Manche Hersteller setzen auf Lacke, andere auf Folien, manche Beschichtungen sind elastisch und lassen die Regentropfen zurückprallen, andere sind hart, damit sie die Tropfen brechen. „Wir werden auch metallische Kappen entwickeln, inklusive Blitzschutz“, betont Buchbach. Ebenso sollen selbstheilende Lacke zum Einsatz kommen. Sie beinhalten mikroverkapselte Wirkstoffe, die in eine Beschichtung eingearbeitet werden. Tritt eine Beschädigung auf, reißen die Mikrokapseln auf und setzen eine Flüssigkeit frei, die den Riss aushärtet. Die Lösungen sollen möglichst lange haltbar und möglichst einfach anzuwenden sein, nicht nur in einem engen Zeitfenster unter idealen Wetterbedingungen.
Zunächst aber geht es darum, die Schädigungsmechanismen besser zu verstehen, den Istzustand zu analysieren und ein Schadenskataster aufzubauen. Möglichst dicht dran an der Realität sollen dazu die Testbedingungen sein. Mit der Schadensanalyse ist im Materialprüflabor neben Stefan Krause auch Cate Lester, Wissenschaftliche Mitarbeiterin am IWES, betraut. Die Amerikanerin war nach ihrem Master in Windenergie an der Technischen Universität Kopenhagen ans IWES gewechselt. Warum sie nach Bremerhaven kam? „Weil dies ein guter Platz für angewandte Forschung zur Windenergie ist! Die Weiterentwicklung von grüner Energie ist mir wichtig.“
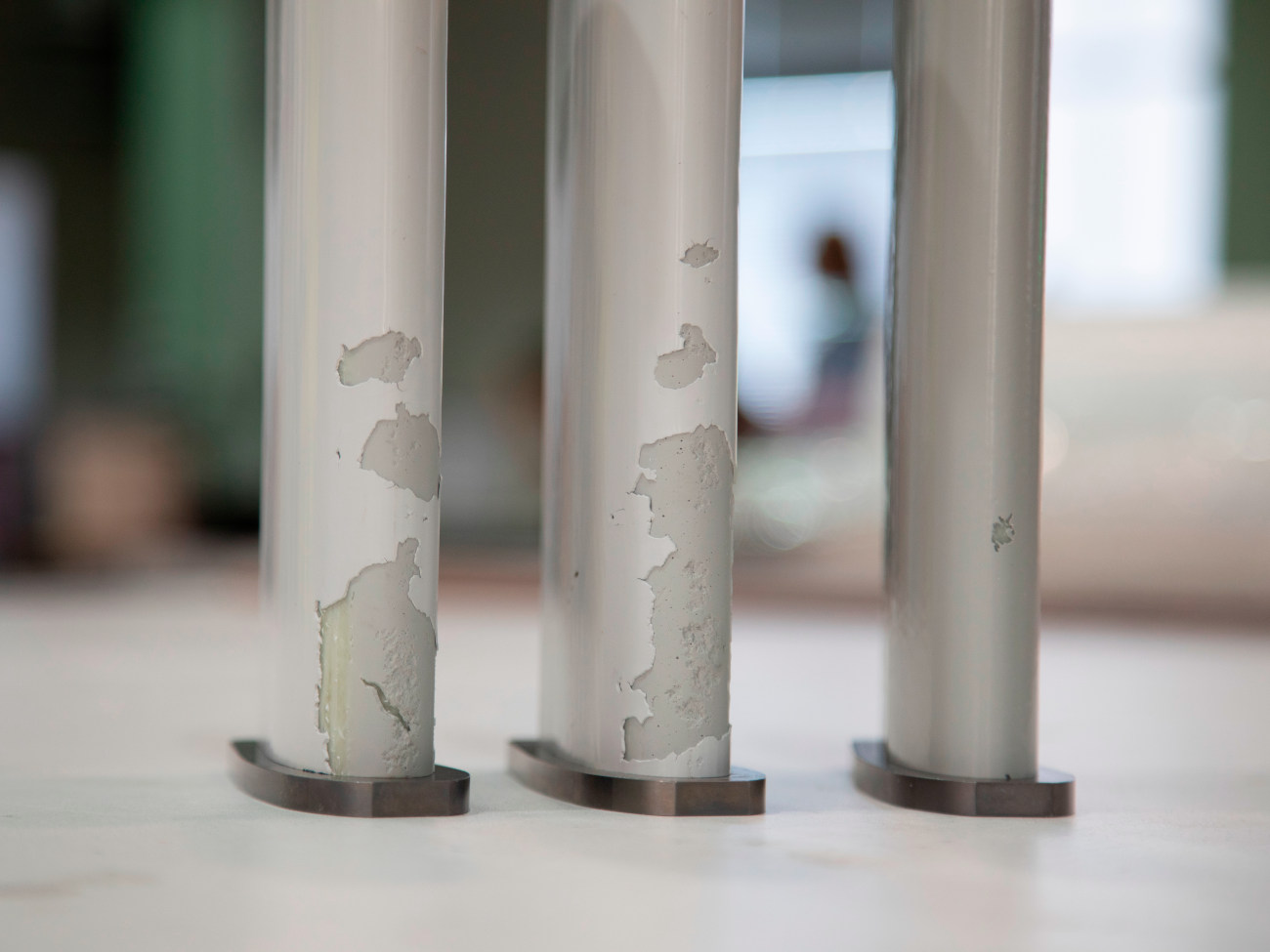
© Jens Lehmkühler
Der Regenerosionsprüfstand ist nur einer von mehreren Prüfständen des IWES. Im selben Areal, im 2023 eingeweihten Rotorblattprüfstand, durchlaufen Rotorblätter mit einer Länge von mehr als 115 Metern zahlreiche Prüfungen, bevor sie in Serie gehen. Rotorblätter sind für die Leistungsfähigkeit, Zuverlässigkeit und Kosteneffizienz einer Windenergieanlage entscheidend. Investitionen in ihre Weiterentwicklung und ihren Schutz sind essenziell. Auf dem Weg in eine klimaneutrale Zukunft ist diese Forschung ein wichtiger Baustein. Zugleich trägt sie zur Stärkung des Standortes Bremerhaven bei, der sich zu einem Zentrum der Windenergieforschung in Deutschland entwickelt hat und Wissenschaftler:innen anzieht, denen die Weiterentwicklung dieser Technologie am Herzen liegt. Zu ihnen zählt neben Cate Lester auch der Oldenburger Stefan Krause. „Die Windenergie“, sagt der Messtechniker, „ist auch technisch interessant.“
„Wir ergänzen uns sehr gut.“ Sascha Buchbach
Am Fraunhofer IFAM wird in den zahlreichen Materiallaboren die Basis für die Nutzung von neuen Werkstoffen in der Windenergie geschaffen. Hier werden Werkstoffkennwerte ermittelt, das thermische Werkstoffverhalten analysiert und Alterungsmechanismen untersucht. Die gewonnenen Erkenntnisse fließen in die Schadensanalyse ein und sind insbesondere für die Entwicklung zukünftiger Materialien wertvoll. Beide Institute, Fraunhofer IWES und Fraunhofer IFAM, kooperieren nicht nur bei MARiLEP. Während das IFAM darauf spezialisiert ist, neue Materialien zu entwickeln, besteht die Expertise des IWES in der Entwicklung und Validierung von Testverfahren. „Wir ergänzen uns sehr gut“, betont Diplomingenieur Buchbach, der in diesen Tagen sein 25-jähriges Jubiläum am IFAM feiert.
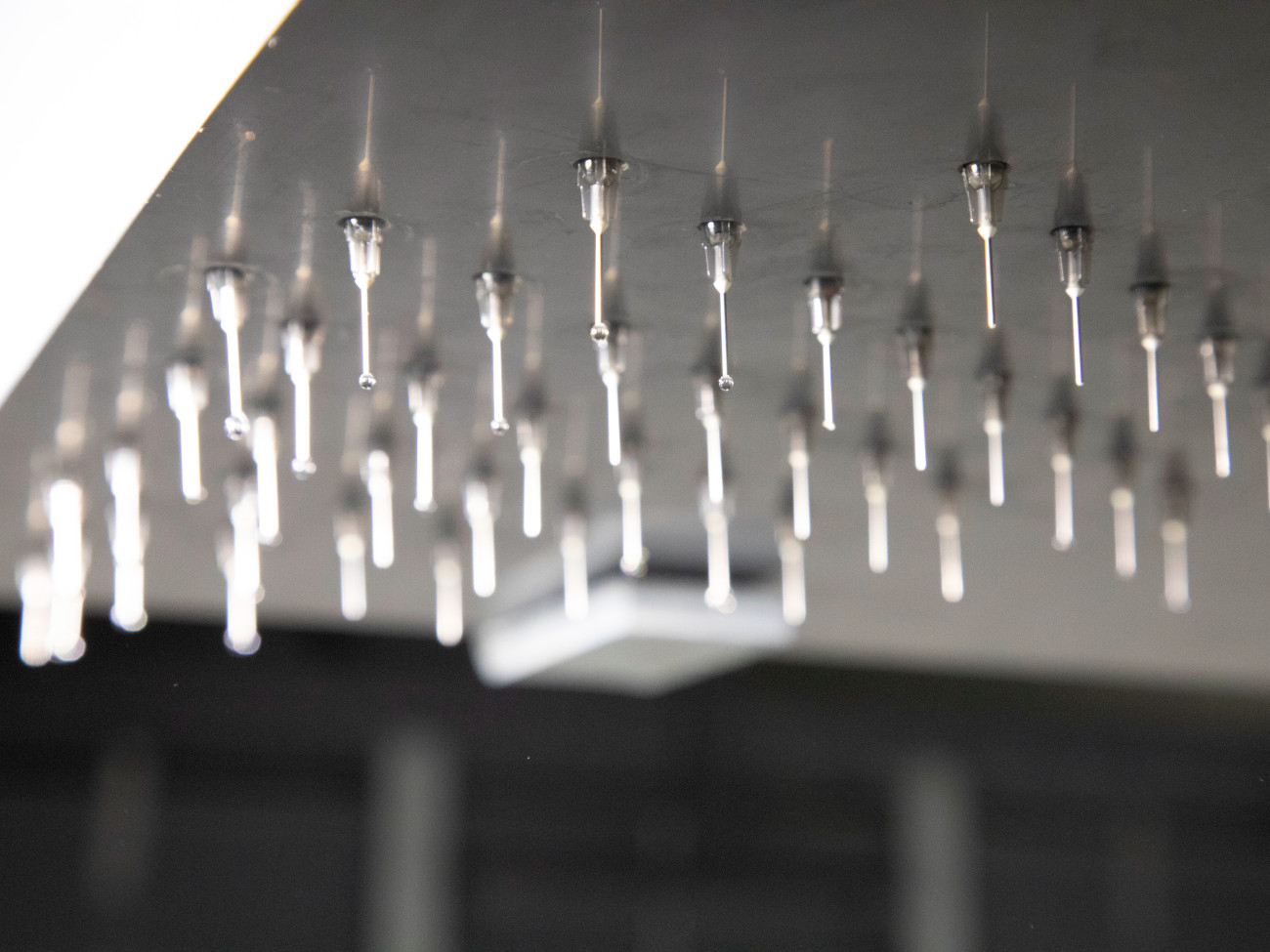
© Jens Lehmkühler
Im Projektkonsortium sind neben der Wissenschaft zudem Hersteller von Beschichtungssystemen für den Erosionsschutz sowie Anwender von Reparaturlösungen in Windparks dabei. „Gemeinsam mit den Partnern neue Materialien und Reparaturkonzepte zu entwickeln, die dann auch in Serienreife gehen – das ist für mich das Spannende an dem Projekt“, betont Buchbach. „Letztlich geht es darum, längere Laufzeiten von Windenergieanlagen zu ermöglichen und die Wartungskosten zu reduzieren.“ Drei Produkte – ein Lack, ein Foliensystem und eine metallische Schutzkappe – sollen im Rahmen von MARiLEP auf den Markt kommen. 2026 könnte es so weit sein. Bis dahin ist das Vorhaben finanziert.
Eine Herausforderung bei den Reparaturlösungen ist deren konkrete Anwendung: Ist die Luft zu kalt, der Wind zu stark oder die Luftfeuchtigkeit zu hoch, sind Reparaturen derzeit nicht möglich. Die neuen Technologien werden das Zeitfenster für die Reparaturen deutlich erweitern. Doch die nötigen Spezialist:innen, die dies offshore ausführen, sind knapp und teuer. Auch für die Lösung dieses Problems hat Buchbach ein Zukunftsszenario im Kopf: Drohnen! Sie könnten die Rotorblätter inspizieren, Schäden feststellen und sie eigenständig reparieren. „Aber dazu ist vorher noch viel Forschungsarbeit notwendig.“
Offshore-Drohnen
Der Ausbau von Windenergieanlagen vor den Küsten geht einher mit einem wachsenden Markt für Inspektions- und Wartungsarbeiten. Mit dem „Offshore Drohnen Campus Cuxhaven“ (ODCC), einer Test- und Entwicklungsinfrastruktur für unbemannte Luftfahrtsysteme, reagiert das Fraunhofer IFAM auf diese wachsende Nachfrage. An dem Standort sollen Offshore-Drohnen gemeinsam mit wissenschaftlichen Partnern und der Industrie weiterentwickelt werden. Forschungsschwerpunkte sind dabei der sichere und effiziente Einsatz von Drohnen bei Offshore-Arbeiten wie Wartung, Inspektion, Reparatur und Vermessung sowie die Entwicklung neuer Antriebs- und Materialschutzkonzepte für den fordernden Einsatz der Fluggeräte unter Offshore-Bedingungen.
Der Artikel stammt aus Impact- Dem Wissenschafts-Magazin der U Bremen Research Alliance
In U Bremen Research Alliance kooperieren die Universität Bremen und zwölf Institute der bundländerfinanzierten außeruniversitären Forschung. Die Zusammenarbeit erstreckt sich über vier Wissenschaftsschwerpunkte und somit „Von der Tiefsee bis ins Weltall“. Das Wissenschafts-Magazin Impact gibt zweimal im Jahr spannende Einblicke in das Wirken der kooperativen Forschung in Bremen.