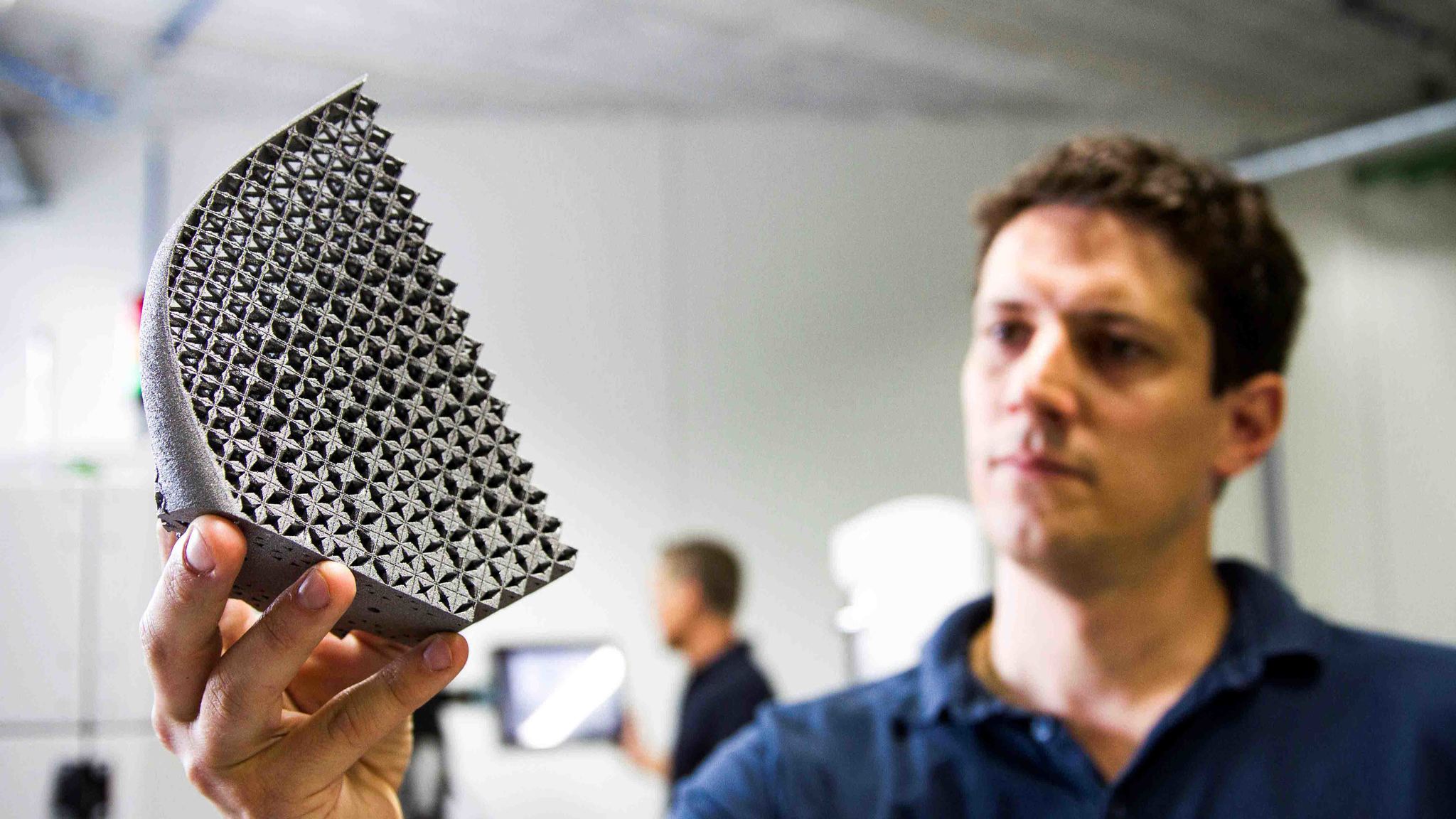
Foto: Materialise GmbH
Wunderwerk aus Metall
Karriere im Doppelpack: Ein Absolvent der Universität und ein belgischer Gastwissenschaftler werden in Bremen durch eine neue Technologie inspiriert – und finden später wieder zusammen
Klar doch, auf solch eine Erfolgsstory ist jede Universität stolz: Ein Studierender und Absolvent macht erst seinen Weg in der Forschung, gründet dann eine eigene Firma und wird später Geschäftsführer des deutschen Standortes eines Weltmarktführers mit einer Niederlassung in Bremen. Dieser Weltmarktführer wiederum ist aus einer Idee entstanden, die vor gut 30 Jahren ganz maßgeblich in einem An-Institut der Universität mitverfolgt wurde. Karriere im Doppelpack also – für den Menschen, für das Unternehmen. Konkret geht es hier um Marcus Joppe, um den 3D-Druck von Metall und um die Firma Materialise.
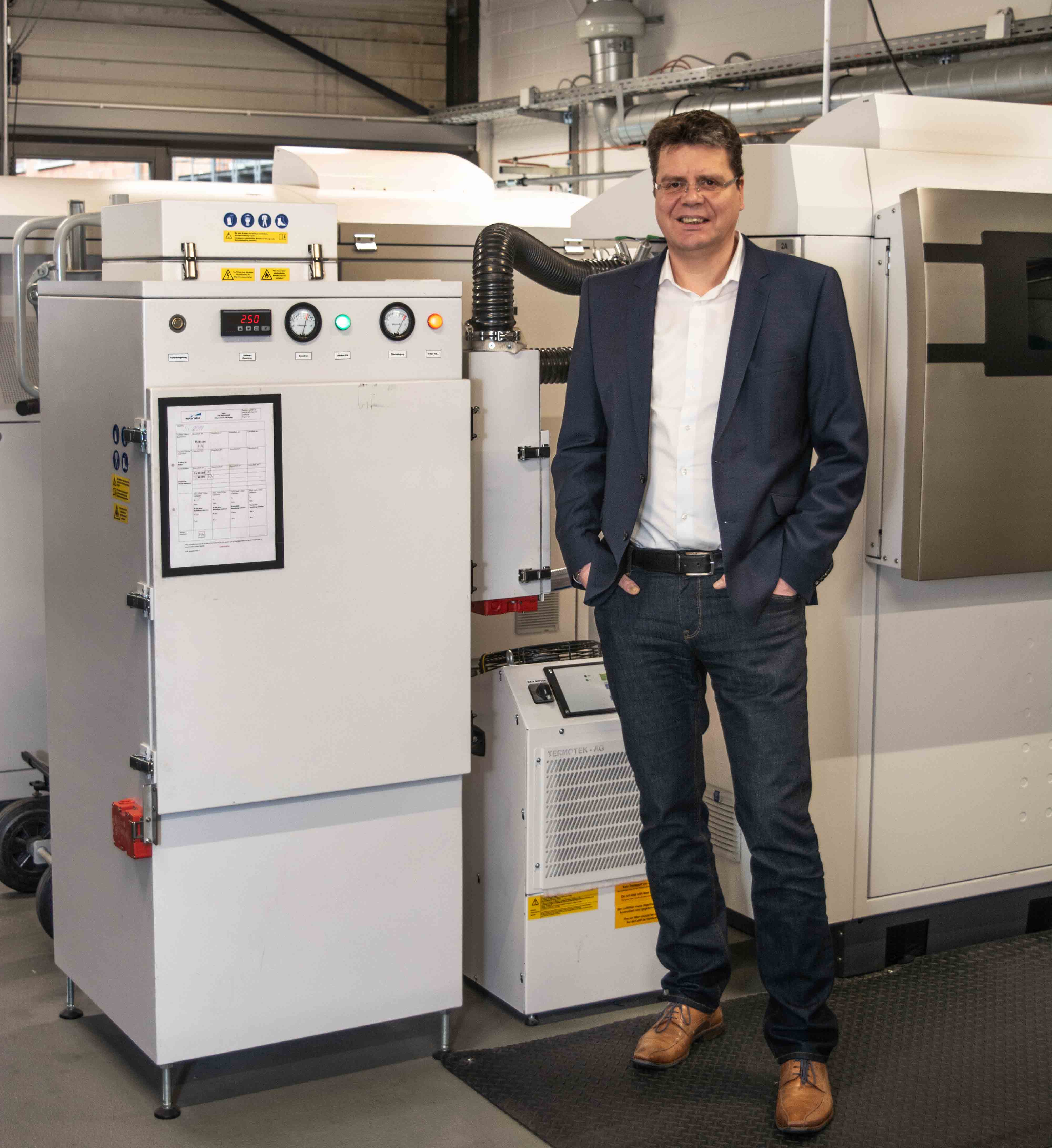
Foto: Kai Uwe Bohn / Universität Bremen
„Da stand ein Zug im Bahnhof, in dem wollte ich sitzen – und nicht irgendwann hinterherwinken.“ Marcus Joppe, Materialise GmbH
Fast 30 Jahre ist es her, dass der Informatik-Student Marcus Joppe, damals Drittsemester, an der Bremer Universität einen Studentenjob suchte. Und fand: Im An-Institut BIBA – Bremer Institut für Produktion und Logistik GmbH arbeitete er fortan mit dreidimensionalen Konstruktionsund Fertigungsprogrammen. Schnell kam er auch mit dem 3D-Druck in Kontakt, und das 20 Jahre, bevor der Hype um das dreidimensionale Drucken so richtig losging. „Das glaubt mir heute kaum jemand, wenn ich erzähle, dass die erste 3D-Druck-Anlage in Europa am BIBA 1989 in Betrieb genommen wurde“, sagt Joppe.
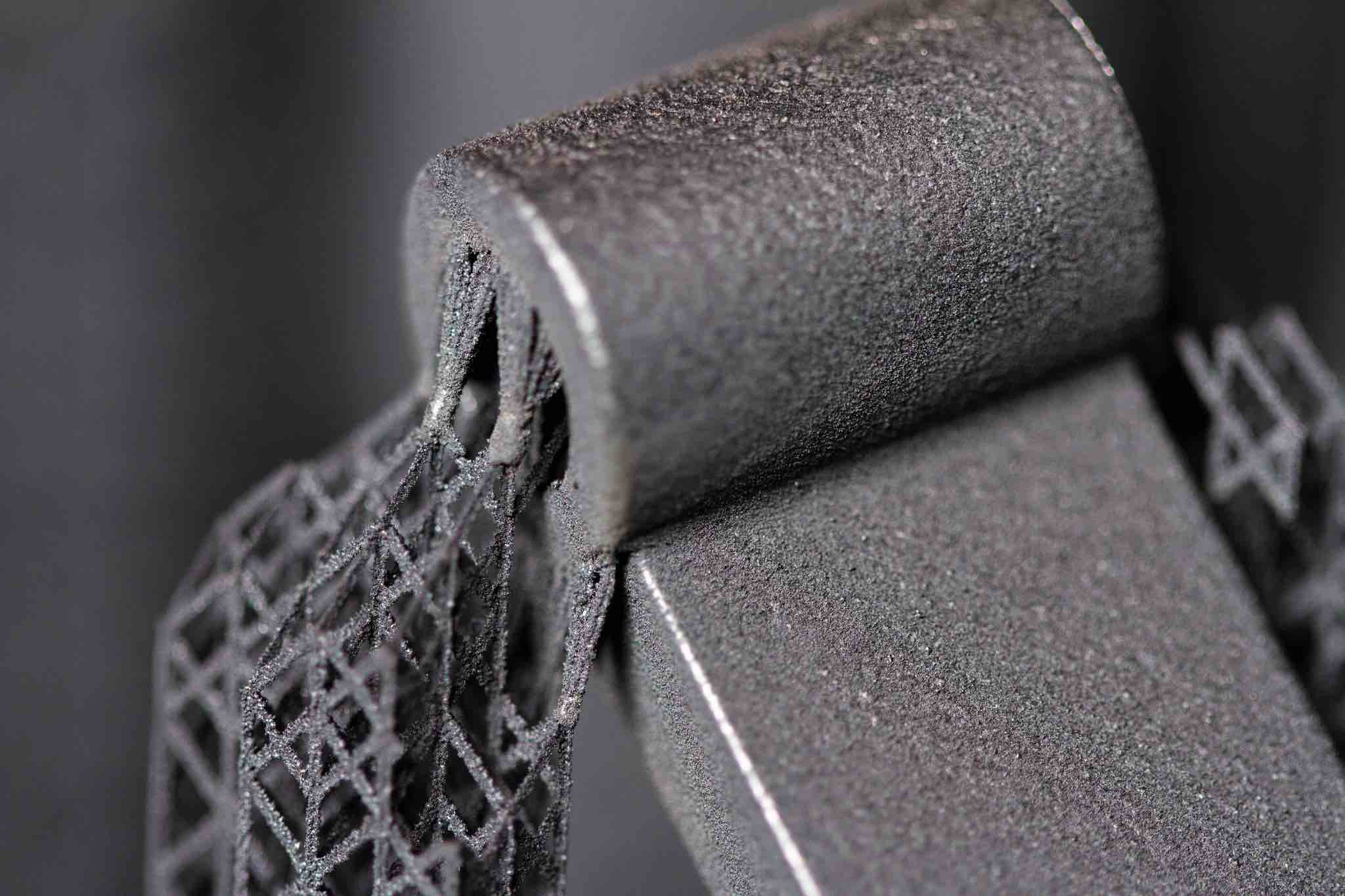
Foto: Materialise GmbH
„Das war schon damals eine tolle Technologie“, erinnert er sich. „Hochinteressant, um Prototypen oder Musterentwürfe herzustellen.“ Aber eben auch noch mit einer Menge Entwicklungsbedarf: „Um Druckjobs vorzubereiten, brauchte man mit den damaligen CAD-Systemen ein bis zwei Wochen. Heute geht das in Minuten.“ Man musste schon die Möglichkeiten des 3D-Drucks erkennen und in die Zukunft schauen können. Einer konnte das – der Belgier Wilfried Vancraen. Der Wissenschaftler der Universität Leuven arbeitete im Rahmen eines europäischen Forschungsprojektes mit dem BIBA zusammen. Dort sah er bei einem Besuchstermin den ersten 3D-Drucker. Der dreidimensionale Druck ließ ihn fortan nicht mehr los. Nach einem weiteren halben Jahr am Forschungsinstitut der belgischen Metallindustrie gründete Vancraen 1990 in seinem Heimatland die Firma Materialise. Sein Ziel: Mit der neuen Technologie durchzustarten.
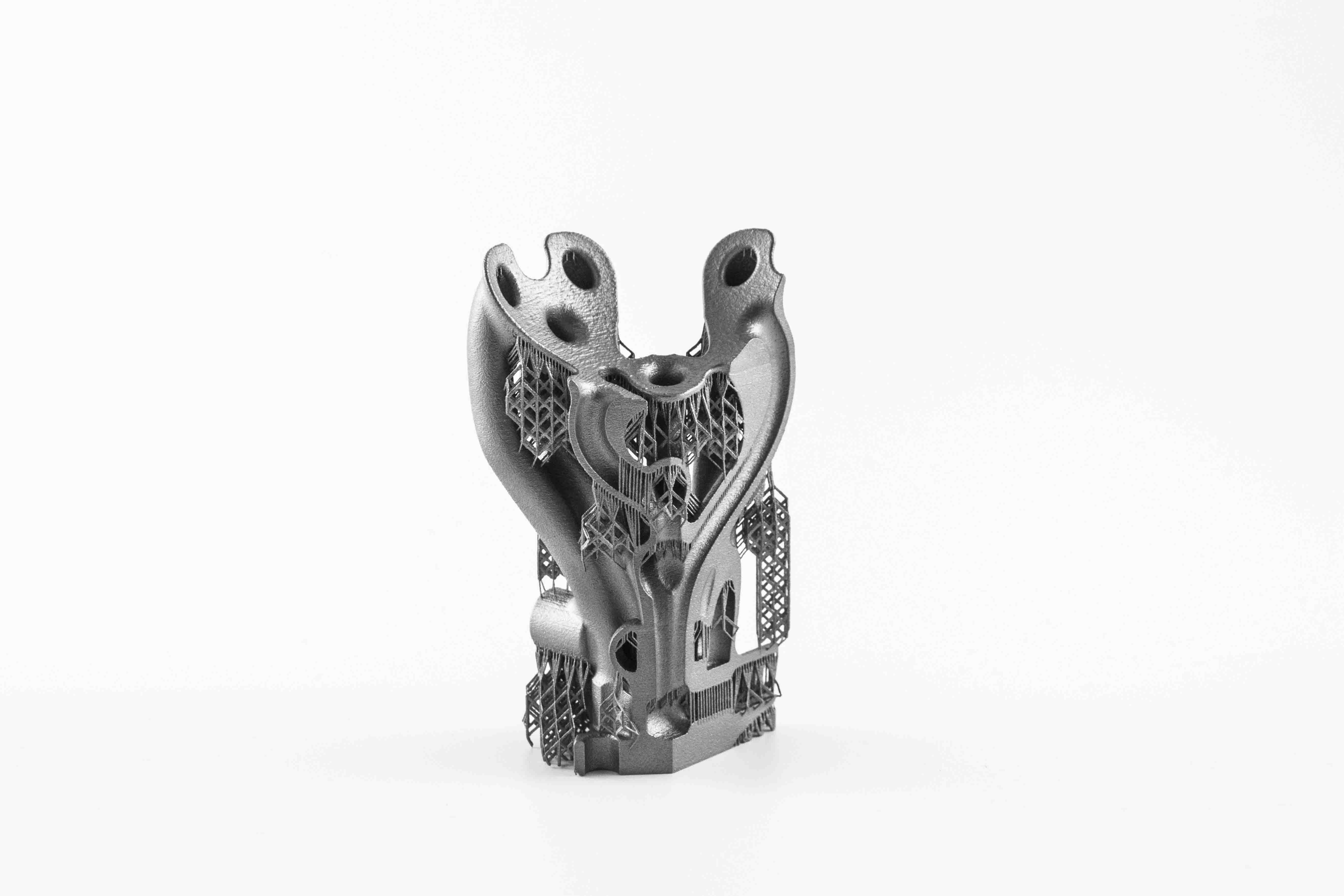
Foto: Materialise GmbH
Zurück zu Marcus Joppe. Der setzte in Bremen seinen Weg als Wissenschaftler fort: Erst der Studentenjob am BIBA, dann das Informatik-Diplom an diesem Institut erarbeitet, schließlich dort wissenschaftlicher Mitarbeiter und sehr bald auch Abteilungsleiter für den 3D-Druck. Fünf Jahre widmete er sich vor allem der Softwareentwicklung – denn ohne eine Datenvorbereitung und Steuerungstechnik, die die fehlerfreie Fertigung im Mikrometerbereich garantieren, bleibt die ganze Idee des dreidimensionalen Druckens nur ein schöner Traum. Schließlich machte sich Joppe selbständig, denn es gab etwas, was ihn im Wissenschaftsbetrieb grundsätzlich störte: „Man erzielt mit viel Energie und Einsatz ein Forschungsergebnis – und dann ist das Projekt beendet, und es geht häufig nicht mehr weiter.“
Die Geschäftsidee gesehen
Marcus Joppe wollte aber, dass es weitergeht: „Ich wusste, dass wir uns mit der BIBA-Software nicht verstecken müssen. Ich habe die Geschäftsidee gesehen.“ 2001 gründete er die auf 3D-Druck-Software spezialisierte Marcam Engineering GmbH, dabei zunächst noch stark vom BIBA unterstützt. Im Bremer Innovations- und Technologiezentrum (BITZ), einer der ersten „Startup-Schmieden“ der bremischen Wirtschaftsförderung, wuchs Joppes Unternehmen bald kontinuierlich. „Wir haben auf die richtige Nische gesetzt, nämlich den 3D-Druck von Metall. Kunststoff war damals schon etabliert, gedruckte Metallprodukte gab es kaum auf dem Markt.“ Das änderte sich langsam – auch durch Joppes Unternehmen, das die Software-Unterstützung für den heranwachsenden Zweig anbot.
Dass der Druck metallischer Teile für bestimmte Bereiche hochinteressant ist, zeigte sich schnell. „Einen geschwungenen Lüftungskanal kann man nicht bohren“, erklärt Joppe. „Bohren geht nur geradeaus. Das macht deutlich, dass durch den Metall-3D-Druck völlig neuartige Komponenten möglich werden – in einem Detailreichtum, der seinesgleichen sucht.“ Und er zeigt einen käfigartigen Metallwürfel, der in seinem Inneren äußerst filigrane Strukturen aufweist: „So etwas kann man nicht fräsen, gießen oder pressen. Das geht nur mit 3D-Druck.“
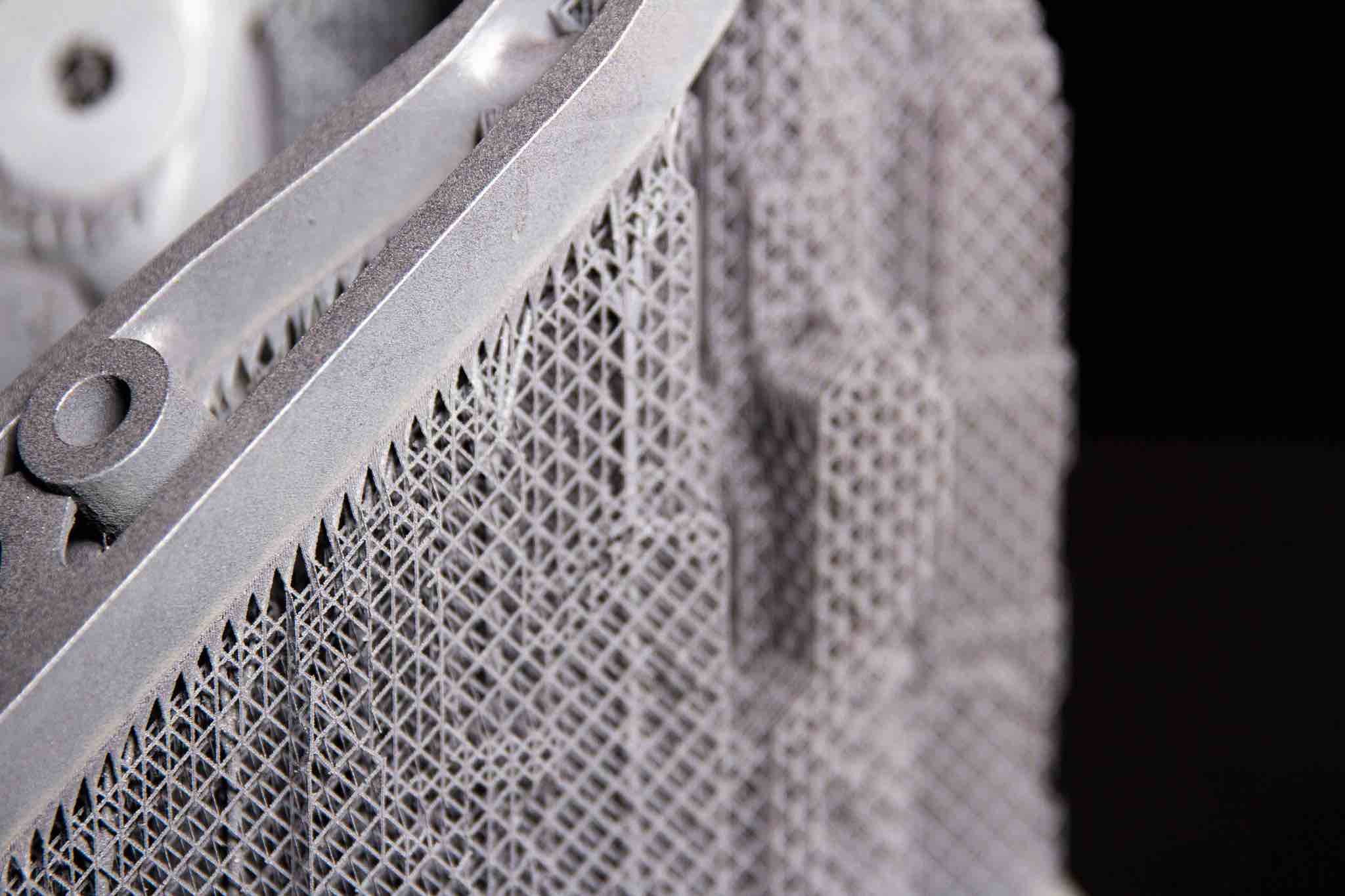
Um 2010 herum begann weltweit endgültig der Boom des dreidimensionalen Drucks, nicht zuletzt getrieben durch einen Hype unter Börsianern. „Marcam stand gut da, aber ich hatte das Gefühl, der Markt wächst schneller als wir. Da stand ein Zug im Bahnhof, in dem wollte ich sitzen – und nicht irgendwann hinterherwinken.“ Joppe hielt Ausschau nach Partnern. Nun kam wieder der Belgier Vancraen ins Spiel: Er hatte Materialise mit hoher Kompetenz im Kunststoffbereich groß gemacht, aber wenig Expertise beim Metalldruck. Die beiden Firmen fanden zusammen, Marcam wurde 2011 ein Teil von Materialise. Es ging sogar noch einmal zurück ins BITZ: Dort eröffnete das Unternehmen einen Produktionsstandort speziell für die Auftragsfertigung von Bauteilen aus Titan und Aluminium. Unikate, Kleinserien und Prototypen werden dort für verschiedenste Industriebereiche, aber auch Privatkunden hergestellt – vom ausgefallenen Schmuckstück über individuelle Hüftimplantate und Querlenkeraufhängungen von Rennwagen bis hin zur zertifizierten Produktion für die Luftund Raumfahrt oder die Automobilindustrie.
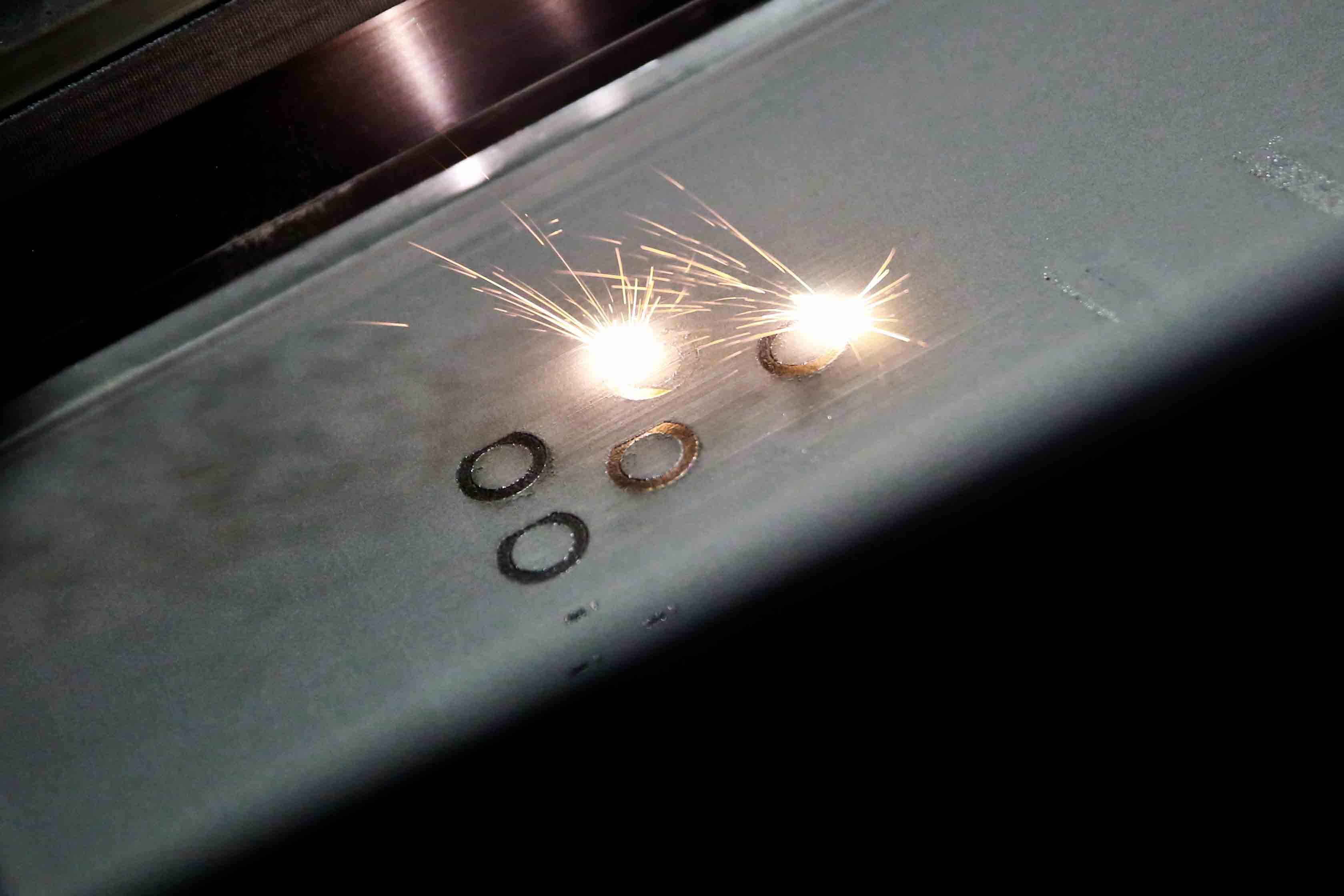
Foto: Materialise GmbH
100er-Grenze im Visier
Mit großem Erfolg. Als die Firma des Uni-Absolventenvor acht Jahren zu Materialise kam, hatte Marcus Joppe zwölf Mitarbeiterinnen und Mitarbeiter. Heute sind es 75, bald will man die 100er-Grenze brechen. „Es läuft“, freut sich Marcus Joppe. Er wird dabei nicht müde zu betonen, wie wertvoll die Ansammlung ingenieurtechnischen Know-hows in der Universität und im Technologiepark für sein Geschäft ist. BIBA, BIAS, IWT, BIMAQ, ISEMP, Fraunhofer-IFAM – hinter diesen Abkürzungen stecken exzellente wissenschaftliche Einrichtungen, deren helle Köpfe untereinander bestens vernetzt sind und im engen Austausch mit der anwendenden Industrie – wie in diesem Fall mit Materialise – stehen. „Wenn wir hier bei uns eine Herausforderung haben, wissen wir sofort, wen wir fragen müssen“, sagt Joppe. „Die Spezialisten, die wir in diesen Momenten brauchen, sitzen in Bremen praktisch um die Ecke.“
Dass Studierende und Nachwuchswissenschaftler der Universität bei Materialise sehr gefragt sind, versteht sich von selbst. Und vielleicht sind ja wieder ein junger Student oder eine junge Studentin dabei, die erst nur einen Job suchen, dann aber ihren Weg machen. Der Chef kann ihnen bestimmt gute Tipps geben.
3D-Druck von Metall: Wie geht das?
Dreidimensionales Drucken ist kein Hexenwerk mehr. Für den spielerischen Hausgebrauch gibt es schon Geräte um 300 Euro mit Kunststoffdraht als Basismaterial. Hochwertige Komponenten für die Industrie werden jedoch immer öfter mit Metallpulver gedruckt, erfordern viel Know-how und sind noch relativ teuer.
Der Druckprozess sieht spektakulär aus: Kleine Blitze – ähnlich denen einer Wunderkerze – zucken unregelmäßig über eine gleichförmig graue Fläche. Wo es geblitzt hat, bleiben dunkel-graue Narben übrig. Lange sind sie nicht zu sehen: Kaum hören die Blitze auf, verteilt ein Schieber eine neue hauchdünne Lage graues Pulver gleichmäßig auf der Oberfläche. Schon geht die Prozedur von vorne los. An den Stellen, die die Steuerungssoftware vorgibt, erhitzt ein Laser auf Hundertstel Millimeter genau das Metallpulver – meist Aluminium, Titan oder eine Titan-Aluminium-Vanadium- Legierung. Das Pulver schmilzt an diesen Stellen, härtet aus und bildet eine von vielen tausend Schichten einer oftmals komplexen Struktur. Dieser Vorgang wiederholt sich immer wieder, stundenlang.
„Additive Fertigung“ nennen die Spezialisten diese Herstellungsweise. Denn anders als bei der „subtraktiven Fertigung“, wo aus einem Metallblock ein Werkstück herausgesägt oder -gefräst wird und Details abgeschliffen oder gebohrt werden, entsteht hier das Produkt Schicht für Schicht. Der Clou dabei: Was gefertigt werden soll, ist bis ins allerletzte Detail individualisierbar. Weil das nicht erhitzte Pulver im Bearbeitungsraum verbleibt, sieht man das Druckergebnis erst ganz am Ende. Bis das überschüssige Pulver abgebürstet wird, umhüllt es das dreidimensionale Produkt. So, wie Wüstensand ein Autowrack verschwinden lassen kann, bleiben auch die hergestellten Werkstücke zunächst verborgen. Willkommener Nebeneffekt: Das verbliebene Metallpulver kann zu 95 Prozent weiterverwendet werden.